Exploring the Diverse Uses of Industrial Diamonds

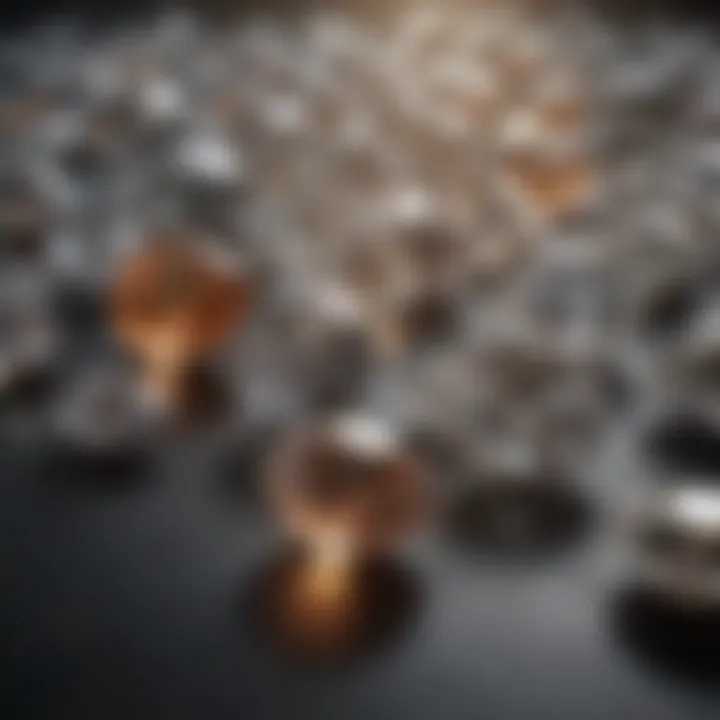
Intro
In the realm of gemstones, the sheer variety is breathtaking. Among these, industrial diamonds stand out not merely for their beauty, but for their extraordinary functionality. Often overshadowed by their more glamorous counterparts, these diamonds play a crucial role across various industries. Their unique properties, which combine hardness, thermal conductivity, and optical characteristics, make them indispensable in several applications, particularly in cutting, grinding, and advanced technology sectors.
In this exploration, we aim to peel back the layers of industrial diamonds by discussing their myriad applications. From ancient uses to modern innovations, their historical significance and current breakthroughs will be unpacked. By shedding light on the fine line between aesthetics and practicality, we cater to both gemstone enthusiasts and industry professionals alike.
Gemstone Overview
Definition of Gemstones
Gemstones are naturally occurring minerals that have undergone a series of processes before they can be categorized as such. Most often, they’re valued for their beauty, rarity, and durability. While many think of gemstones in a jewelry context, it is essential to recognize that industrial diamonds serve a different function entirely. Rather than ornamental, these diamonds are crafted for performance-driven applications, which are equally remarkable.
Classification of Gemstones
Gemstones generally fall into various categories based on their mineral compositions and characteristics. Industrial diamonds can be classified under the broader category of diamonds, often classified by their quality and intended purpose.
- Natural Diamonds: Formed over millions of years, these are mined from the earth.
- Synthetic Diamonds: Created through artificial processes; they mirror the characteristics of natural diamonds.
- Industrial Diamonds: Designed specifically for cutting and grinding tools, lacking the sparkling qualities associated with gems.
Industrial diamonds, while sharing the same carbon structure as their decorative cousins, possess different utilizations in industries such as electronics and construction, emphasizing function over form.
"Industrial diamonds might not adorn a finger, but their contribution to technology and manufacturing is priceless."
This categorization serves as a foundation for understanding the distinctive roles that industrial diamonds fulfill, while also hinting at the revolutionary technologies they help to foster.
Prelude to Industrial Diamonds
Industrial diamonds are not just the stuff of sparkling jewelry; they have carved out a niche in various sectors, serving roles that highlight their extraordinary attributes. These diamonds stand out from their gem-quality counterparts in several key ways, making them essential in fields such as manufacturing, construction, and technology.
When we talk about industrial diamonds, we refer to diamonds that are specifically manufactured or sourced for their utility rather than their aesthetic appeal. Their hard, durable nature and thermal conductivity make them ideal for a variety of applications, such as cutting, grinding, and drilling. Thus, their importance cannot be understated; they are, in many respects, the backbone of modern industrial processes.
Moreover, understanding the characteristics of industrial diamonds helps industries harness their properties effectively, leading to enhanced performance and cost efficiency. Here, we look into what exactly sets industrial diamonds apart and how they compare to the more commonly known gem quality diamonds.
Definition and Characteristics
Industrial diamonds are defined as diamonds that are utilized in industrial applications rather than for ornamental purposes. They come primarily from the same geological processes as gem-quality diamonds but are not classified based on their visual appeal or clarity. Instead, their value lies in their hardness, thermal properties, and chemical stability.
Characteristics include:
- Exceptional Hardness: Industrial diamonds register the highest level of hardness on the Mohs scale, graded at 10, making them invaluable for cutting and drilling applications.
- Thermal Conductivity: They can withstand high temperatures, which is crucial for processes that require heat resistance.
- Chemical Resistance: Industrial diamonds are inert and resist various chemicals, making them suitable for demanding environments.
Some examples of industrial diamond forms are diamond abrasives, diamond grits, and diamond discs, each engineered for specific tasks in manufacturing and construction settings. Their capabilities allow specialists to enhance their operational efficiency.
Comparison with Gem Quality Diamonds
Although both industrial and gem quality diamonds originate from the same mineral, their characteristics diverge significantly in terms of purpose and valuation. Gem quality diamonds are prized for their brilliance, clarity, and color, often fetched at astronomical prices. On the other hand, industrial diamonds lack the aesthetic qualities required for jewelry, thus are much more affordable and abundant.
Key differences include:
- Purpose: Gem quality diamonds are sought after for adornment, while industrial diamonds are manufactured for utility.
- Value: The pricing spectrum differs greatly. While a gem diamond's worth is based on beauty and demand, industrial diamonds derive value from their performance capabilities.
- Processing: The grading of gem diamonds involves complex criteria such as cut, color, clarity, and carat weight, whereas industrial diamonds are evaluated based on their size, shape, and purity for specific applications.
As such, the evolving landscape of industrial diamonds highlights their importance in various industries and research initiatives. With advancements in technology, the industry continues to explore innovative methods to manufacture and utilize these diamonds, thus enhancing their applications and market reach.
Historical Context of Industrial Diamonds
The journey of industrial diamonds charts a remarkable course through history, a tapestry woven with innovation, necessity, and adaptation. Understanding this context offers insight not only into their current applications but also the evolution of industries reliant on these hard-as-nails gemstones. Historically, diamonds have been revered for their beauty, yet it is their unparalleled hardness that has made them truly invaluable in industrial settings. This section will take a closer look at the evolution of industrial diamond production and highlight key milestones that have shaped the industry.
Evolution of Industrial Diamond Production
When we trace the roots of industrial diamond production, we find the initial use of diamonds primarily for decorative purposes. However, around the late 19th century, a groundbreaking realization dawned upon manufacturers: these gemstones could be harnessed as tools. The first commercial use of industrial diamonds is often credited to the need for better cutting and drilling tools, particularly as infrastructures and machinery were rapidly developing.
Key Developments Over Time:
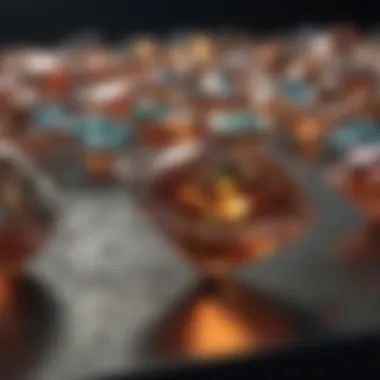
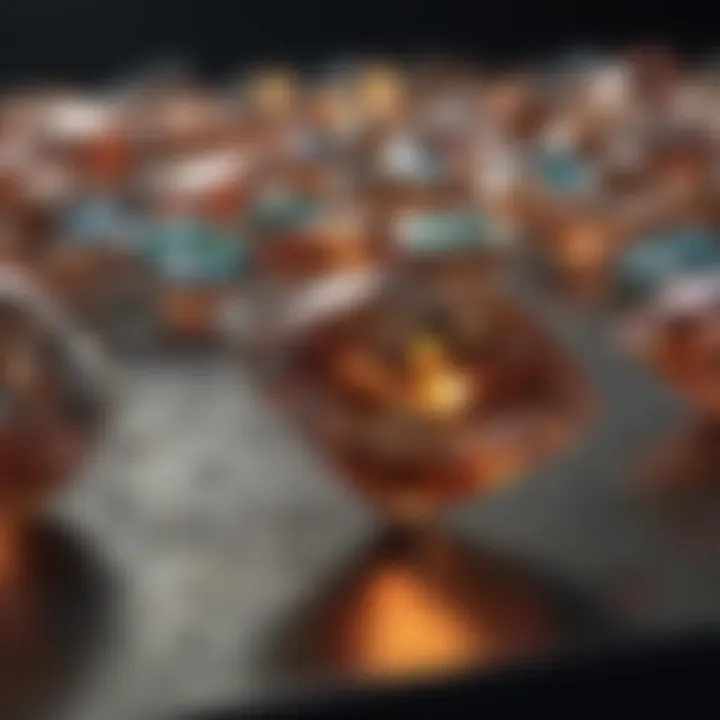
- 1900s: The first synthetic diamonds were created, opening the floodgates for mass production. Instead of relying solely on naturally occurring diamonds, manufacturers began to experiment with high-pressure techniques to create diamonds from carbon.
- 1930s - 1940s: World War II drove significant advancements in diamond synthesis technologies, as nations scrambled for improved drilling tools to extract resources quickly.
- Post-War Era: In the decades following, industries like oil and gas, construction, and mining increasingly adopted industrial diamonds, along with new applications in metallurgy and electronics.
By the late 20th century, industrial diamonds had firmly established themselves as a cornerstone resource. The enhancement in manufacturing processes and the exploration of novel applications breathed new life into the diamond industry, turning these stones into a vital part of economic development.
Key Milestones in the Industry
The industrial diamond sector has experienced notable milestones that have redefined its landscape. At different intervals, technological advances have transformed production methods and broadened applications. Some highlights include:
- 1960s: The introduction of diamond-coated tools brought forth precision and efficiency in operations, changing paradigms in manufacturing.
- 1970s: The creation of diamond grinding wheels made it possible to achieve finer finishes on materials, leading to a revolution in manufacturing standards and practices.
- 21st Century: Innovations continue to surge, particularly with the advancement of synthetic diamond technologies, driving down costs and enhancing availability.
As a consequence of these milestones, industrial diamonds are now indispensable not just in drilling and cutting, but also in applications that were once deemed impossible, such as in the development of new technologies across various fields. With increasing competition in global markets and sustainability concerns, the historical context presents a rich tapestry of adaptability and resilience, paramount for understanding how these diamonds have maintained relevance today.
"The path of industrial diamonds has been paved by the continuous quest for better, faster, and more efficient means of production, embodying the spirit of human ingenuity."
With such a foundation, the narrative of industrial diamonds flows into their present applications and the exciting possibilities that lie ahead.
Cutting Tools and Abrasives
Cutting tools and abrasives play a crucial role in industries where precision and performance are non-negotiable. Industrial diamonds, known for their hardness and durability, slot into this category seamlessly. Their ability to cut, grind, and polish materials is unparalleled, which enhances efficiency and finishing quality in manufacturing processes. As the need for precise engineering grows, so does the prevalence of industrial diamonds in tools tailored for specific applications. Thus, understanding the various aspects of cutting tools and abrasives, especially those made from diamonds, is paramount to grasping how these materials impact industrial operations.
Applications in Manufacturing
The role of diamond tools in manufacturing is multifaceted. From automotive to aerospace, various sectors benefit from the use of diamond-tipped tools that ensure high-accuracy outcomes. These tools not only improve production rates but also decrease wear and tear due to their inherent toughness. Industries that require a high level of precision, such as electronics and medical devices, have started migrating towards diamond-based tools.
Here's how diamond tools enhance applications in manufacturing:
- Increased Efficiency: The superior cutting ability of diamonds permits faster processing speeds, translating to significant time savings in production.
- Enhanced Precision: Tools made with industrial diamonds can achieve tighter tolerances, making them ideal for tasks requiring high precision.
- Longer Tool Life: Due to their hardness, diamond tools exhibit increased longevity, reducing the need for frequent replacements and thus lowering overall operational costs.
Types of Cutting Tools
In the realm of cutting tools, two prominent forms that put industrial diamonds to good use are diamond blades and diamond wheel tools. Each type serves distinct purposes and suits different applications while leveraging the advantages of diamonds.
Diamond Blades
Diamond blades are essential tools in construction and stone cutting. The key characteristic of these blades is their segmented or continuous rim, which is embedded with diamond particles. This design enables the blades to cut through hard materials like concrete, marble, and granite with remarkable efficiency. Their popularity stems mainly from their superior cutting performance, and they tend to produce smoother cuts than traditional blades.
- Unique Feature: Diamond blades maintain their sharpness longer than standard steel blades, reducing the need for frequent sharpening.
- Advantages: They minimize dust and debris during cutting, which is a significant benefit in indoor environments. Additionally, the reduced friction results in less heat generation, prolonging the tool’s lifespan.
- Disadvantages: While offering great benefits, diamond blades can be more expensive upfront compared to regular blades. However, their longevity can offset this initial investment over time.
Diamond Wheel Tools
Diamond wheel tools are integral for grinding and finishing processes, particularly used in the shaping of hard materials like ceramics, glass, and composite materials. These tools are designed with diamond particles bonded to the surface, enabling them to finely grind surfaces with precision and speed.
- Key Characteristic: The bond systems for diamond wheel tools can vary, influencing the tool’s performance based on the materials it’s used on.
- Why It’s Beneficial: Their ability to grind incredibly hard surfaces makes them an ideal choice for industries that cannot afford imperfections in their products.
- Advantages and Disadvantages: Their advantages include superior grinding efficiency and the ability to produce exceptional surface finishes. However, they are often compared with other materials, which can sometimes lead to misconceptions about their effectiveness and appropriateness for various jobs.
"Diamond blades and wheels not only have cutting precision but also provide an unrivaled edge in efficiency, making them indispensable in modern manufacturing."
As we continue to explore the capabilities of industrial diamonds, it’s clear that tools and abrasives formed from them provide not just functional benefits but also strategic advantages to various industries.
Drilling and Mining Applications
In the realm of industrial diamonds, drilling and mining applications hold a fundamental position. This section explores how diamonds contribute significantly to efficient resource extraction, discussing specific techniques that leverage the inherent qualities of these stones. Given their exceptional hardness and thermal conductivity, industrial diamonds shape the industry's approach to resource recovery.
Drilling Techniques Utilizing Diamonds
One of the standout applications of industrial diamonds in drilling is the use of diamond drill bits. These tools are engineered to provide superior penetration capabilities in hard rock formations. As opposed to conventional steel bits, diamond bits can tackle tougher materials, thus reducing the time and cost of drilling operations.
- Core Drilling: Typically employed for geological exploration, this method uses diamond-tipped drill bits to retrieve core samples. The precision of the diamond bits ensures that the samples maintain their structural integrity, crucial for accurate analysis.
- Rotary Drilling: Utilized somewhat widely in oil and gas exploration, this method features diamond bits that rotate and cut through the earth's crust. The durability of diamond allows for extended drilling periods without the need for frequent replacements.
Interestingly, the diamond's microscopic hardness lets manufacturers develop bits with varying characteristics to suit different geological conditions. For instance, softer bindings might go for drilling through limestone while harder ones tackle granite.
Impact on Resource Extraction
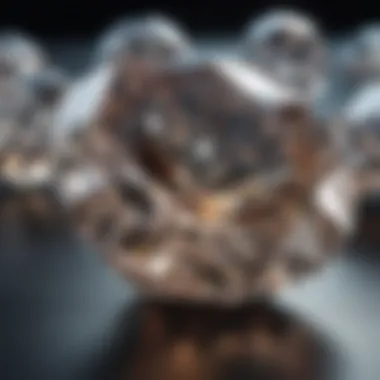
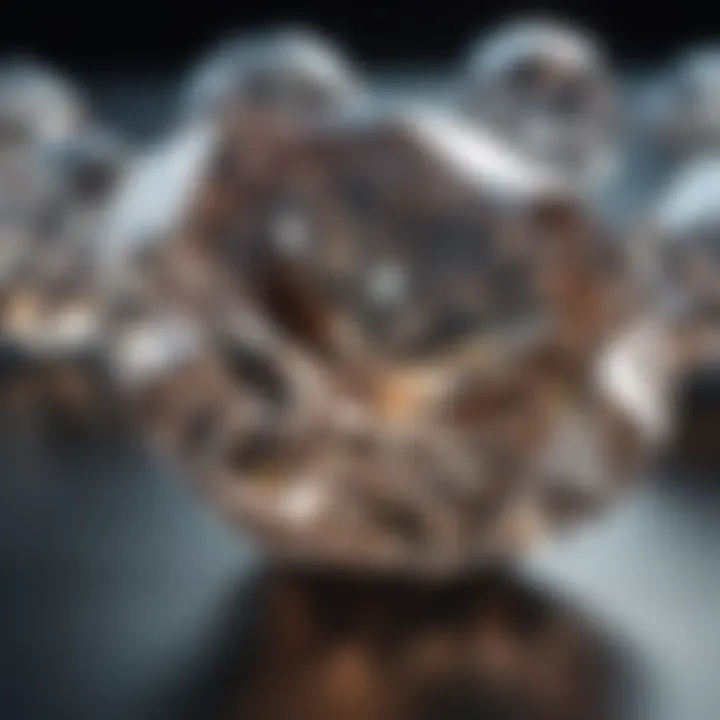
The role of industrial diamonds in resource extraction extends beyond just providing tools. Their integration into drilling and mining processes has far-reaching benefits:
"The application of industrial diamonds in drilling and mining not only enhances productivity but also paves the way for sustainable practices."
- Increased Efficiency: By utilizing diamond-based tools, mining companies enhance drilling efficiency. As these diamonds cut through tough materials with ease, operations can maintain higher speeds and lower costs.
- Reduced Environmental Footprint: Minimizing the number of drill bit replacements leads to lesser waste. Many modern drill bits are designed to be reused, promoting a more sustainable approach to mining operations.
- Better Resource Identification: The precision drilling with diamond bits allows for more accurate geological surveys. This means companies can make informed decisions, reducing unnecessary excavation and resource depletion.
- Enhanced Safety: When operations employ diamond drilling methods, there's typically less vibration and noise involved. This can translate to a safer working environment for miners, enhancing overall site safety.
The advent of industrial diamonds in drilling marks a pivotal shift, promising innovative methods for the extraction of resources. As the industry evolves, the focus remains anchored in finding more sustainable and efficient approaches, with diamonds at the forefront of this endeavor.
Polishing and Finishing Processes
Polishing and finishing processes are crucial steps in utilizing industrial diamonds. These stages ensure that materials and surfaces reach optimal smoothness and shine. With an emphasis on precision and quality, polishing can enhance the functionality and aesthetics of finished products. Not only does it create visually appealing surfaces, but it also plays a significant role in the performance of tools and components across various industries.
In industries such as aerospace and electronics, having a polished finish goes beyond mere aesthetics; it impacts performance. For instance, a smooth surface reduces friction, which can lead to improved efficiency in machinery. Thus, the role of polishing in enhancing operational durability cannot be overstated.
Diamond Powders in Polishing
Diamond powders are the backbone of many polishing applications. They are finely grinded industrial diamonds that come in various mesh sizes, allowing for a range of abrasive qualities. These powders can be mixed with lubricants or suspensions to provide effective finishes on different surfaces, whether they be metals, glass, or ceramics.
- Advantages of Diamond Powders:
- Applications of Diamond Powders:
- Superior Abrasiveness: Due to their hardness, diamond powders outperform most other abrasive materials, making them ideal for demanding applications.
- Versatility: They can be adapted for various uses, from polishing delicate optics to heavy-duty grinding in construction.
- Longevity: Unlike other abrasive materials that wear down quickly, diamond powders maintain their properties longer, leading to cost-effectiveness over time.
- Glass and Ceramics: Used to achieve mirror-like finishes.
- Metals: Essential in tool manufacturing, ensuring smooth and precise edges.
- Electronics: In semiconductor production, diamond powders are vital for polishing wafers.
Diamond powder is not just a luxury; it is a necessity for achieving the high level of finish that many industries demand today.
Applications in Electronics and Optics
In the realm of electronics and optics, industrial diamonds play a vital role beyond simple structural components. Their unique properties lend themselves to specialized tasks that require exact accuracy and heat-resistance.
- Semiconductor Manufacturing:
- Optical Devices:
- Coatings and Films:
- Diamonds serve as crucial substrates for the production of high-frequency and high-power electronic devices. Their thermal conductivity allows for efficient heat dissipation, preventing overheating during operation.
- Diamonds are used in various optical applications, from lenses to beam splitters. Their ability to withstand heavy wear while maintaining clarity makes them ideal for high-precision imaging systems.
- Thin diamond films are used to enhance durability and scratch resistance on optical surfaces. These films do not only maintain transparency but also provide protective layers that extend the lifespan of sensitive equipment.
Understanding the multifaceted uses of industrial diamonds, especially in polishing and finishing, shows their importance in modern manufacturing and technology. As industries continue to demand higher-quality finishes and more durable components, the role of diamond-based applications in these sectors is likely to expand further.
Emerging Technologies and Innovations
Emerging technologies surrounding industrial diamonds have been catching fire in recent years. The versatility of these diamonds opens up a world of innovations, fueling advancements that can shift traditional applications into uncharted territories. As industries continuously strive for performance improvements and sustainability, understanding the role of industrial diamonds in these technologies is crucial. It’s not just about their physical properties anymore—there’s a wave of new potential that researchers and technologists are just beginning to tap into.
Diamond-based Electronics
The realm of electronics is where industrial diamonds are truly carving a niche. Diamonds, particularly synthetic ones, exhibit exceptional thermal conductivity, a characteristic that can be critically beneficial in electronic devices. With devices becoming increasingly compact and powerful, the heat generated poses a significant challenge. Diamonds can efficiently disperse this heat, preventing components from overheating.
For instance, diamond field-effect transistors (FETs) are on the frontier of creating faster and more efficient electronic circuits. Unlike traditional silicon-based components, diamond FETs operate at higher voltages and can withstand greater temperatures without degradation.
Some notable applications include:
- High-Power Electronics: Used in devices like radar and satellite transceivers, where managing heat is paramount.
- Optical Sensors: Diamonds can enhance light absorption and transmission, making them ideal for sensor technology.
However, challenges remain. The cost of synthetic diamond production can be intimidating, with some manufacturers struggling to meet the rising demand. Yet, innovative approaches to diamond synthesis could pave the way for broader adoption in electronics going forward.
Advancements in Synthesis Techniques
The synthesis of industrial diamonds has evolved significantly, with novel techniques reducing costs and enhancing quality. One approach making waves is Chemical Vapor Deposition (CVD). This method allows diamonds to grow on various substrates, leading to increased flexibility in manufacturing applications.
Benefits of enhanced synthesis techniques include:
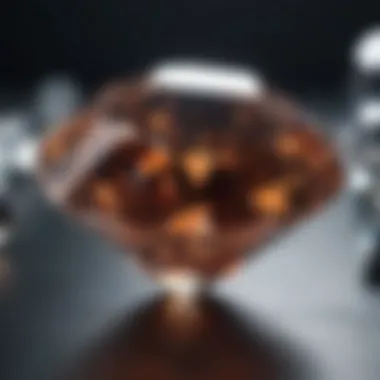
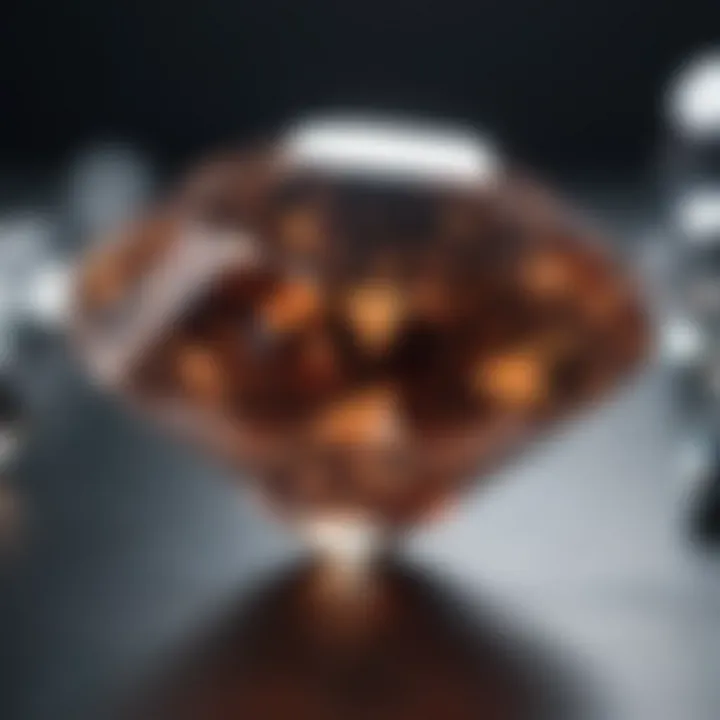
- Tailored Properties: By adjusting the synthesis conditions, manufacturers can design diamonds with specific electrical, optical, and thermal properties.
- Scalability: The CVD process can produce large amounts of diamonds at a faster rate, which is vital in meeting industrial needs.
Interestingly, the idea of using waste materials as a part of the diamond synthesis process is gaining traction. By incorporating carbon from organic waste, the environmental footprint can be reduced. It's a win-win, providing a use for waste and creating material that's essential for several high-tech applications.
Overall, innovations in synthesis techniques not only lower production costs but also expand the horizons for how diamonds can be utilized in technology sectors. As more industries recognize the significant potentials, the future of diamond applications seems very bright.
Industrial Diamonds in Research and Development
In the ever-evolving landscape of modern science and technology, the role of industrial diamonds extends beyond their traditional uses. Through innovative applications in research and development, these diamonds are not merely utilitarian; they are poised at the forefront of breakthroughs across various fields. From analytical tools to potential new applications that could reshape industries, understanding this facet reveals their essential nature in advancing knowledge.
Analytical Applications
Industrial diamonds find significant utility in analytical applications, mainly due to their exceptional hardness and thermal conductivity. These properties make them valuable in creating high-precision instruments essential for research laboratories and industrial enterprises.
- Cutting-edge Sensors: Diamonds are used in sensors that measure physical properties like pressure and temperature with remarkable precision. For example, the development of diamond-based piezoelectric sensors is a hot topic. These sensors come in handy in fields like geophysics, where measuring subtle changes can unlock vital environmental data.
- Drug Delivery Systems: Diamonds can be engineered at the nanoscale and incorporated into drug delivery mechanisms. Their biocompatibility allows them to interact with biologically active materials, providing a platform to enhance drug solubility and targeted therapy approaches. Researchers leverage this characteristic for effective cancer treatments and other medical advancements.
- Spectroscopy: In spectroscopic applications, diamonds serve as optical windows that provide high-quality results in various methods like Raman spectroscopy. This enables the detailed study of materials, making it a prime tool for chemists and physicists alike.
Potential Future Uses
Looking ahead, the future promises a horizon of possibilities for industrial diamonds in diverse sectors. As research pushes boundaries, several potential applications emerge:
- Quantum Computing: One of the most exciting prospects lies in using diamonds for quantum computing. Their unique properties allow the creation of quantum bits or qubits, crucial for building next-generation computing systems. This could lead to dramatically faster processing capabilities.
- Photonics: Advances in diamond photonics can greately influence telecommunications. Diamonds can be used in the manufacture of highly efficient lasers and optical devices. This might pave the way for more effective communication systems and lasers that are compact and powerful.
- Energy Storage: Researchers are exploring the use of diamond structures in energy storage solutions, like batteries and supercapacitors. Their thermal and electrical properties could enhance energy capacity and efficiency.
- Nanotechnology: The integration of diamond nanostructures offers endless possibilities in materials science, influencing the creation of lighter, stronger materials with superior properties. This can resonate throughout consumer products, electronics, and beyond.
"Industrial diamonds are not just tools—they are an integral part of our scientific progress fabric, pushing the boundaries of what we can achieve."
In summary, the utility of industrial diamonds in research and development signifies a potent blend of tradition and innovation. Their role is foundational to advancements that could redefine industries, highlighting the continued importance of these remarkable materials. Understanding these complex interactions paves the way for exciting future developments that promise to impact various fields profoundly.
Environmental and Economic Considerations
As the industrial diamond sector expands, understanding the balance between environmental responsibilities and economic impacts becomes crucial. This section provides insight into how sustainable practices are not just beneficial but necessary for the longevity of the industry, alongside exploring the economic contributions that industrial diamonds make in various sectors. The synergy between these themes represents not just a challenge, but an opportunity for innovation in production and processing techniques.
Sustainable Practices in Diamond Production
The shift towards sustainability in diamond production is not merely a trend; it's a response to the pressing demands of climate change and resource management. As industrial diamonds are predominantly created from geological formations, their extraction and manufacturing need careful oversight to reduce environmental impact.
- Mining Techniques: Methods now lean towards eco-friendliness, focusing on minimizing land disruption and preserving biodiversity. Modern mines implement technologies that reduce water usage and recycle waste materials effectively.
- Synthetic Diamonds: The rise of synthetic diamonds presents a game-changer. Lab-grown diamonds offer an alternative that doesn't rely on traditional mining practices. This method significantly lowers environmental degradation, as the energy used in their creation, while still substantial, remains less invasive than traditional mining.
- Ethical Sourcing: Adopting stringent ethical standards ensures that the diamonds sourced have a minimal carbon footprint. Companies are increasingly turning towards carbon offset programs, aiming to balance their environmental impact with their production needs.
These practices not only protect the environment but also enhance corporate reputations. Firms adopting such measures can stand out in a marketplace that becomes progressively conscious of ethical consumption. In turn, this can lead to better customer loyalty and brand value.
Economic Impact of the Industrial Diamond Sector
The industrial diamond sector plays a pivotal role in various economies worldwide. Its multifaceted applications span industries from manufacturing to technology, showcasing its vast economic significance.
- Job Creation: Mining, manufacturing, and research entangle to create thousands of jobs globally. Local economies, particularly in regions rich in natural resources, thrive on the diamond industry's presence, providing livelihoods and opportunities.
- Market Growth: The demand for industrial diamonds continues to rise. Applications in cutting, grinding, and even advanced technology fields such as electronics reflect this trend. Reports indicate a steady growth rate in the diamond market, emphasizing its lasting relevance in our industrial landscape.
- Global Trade: The international trade dynamics of industrial diamonds drive economies. Countries known for diamond production see significant foreign investments, bolstering their economies and fostering trade relationships.
"Sustainability in production is not just a responsibility; it’s an opportunity for innovative advancement in the diamond industry."
In summary, the sustainable practices and economic impacts of the industrial diamond sector illustrate why this debate is vital. As stakeholders in this field, understanding these nuances will serve to harmonize profitability with environmental responsibility.
End and Future Outlook
The exploration of industrial diamonds reveals a rich tapestry of applications that span multiple sectors, showcasing their formidable versatility and resilience. As we draw this article to a close, it's essential to underscore the significance of understanding both the current uses and the future trajectory of this unique material.
Summary of Key Insights
Industrial diamonds are not just assets confined to traditional manufacturing processes; they form the backbone of several innovative technologies.
- Applications Across Industries: From cutting tools to electronics, the role of industrial diamonds is paramount. Their strength and wear resistance make them unparalleled in creating durable products.
- Environmental Implications: Sustainable diamond production is increasingly becoming a focal point. Industry players are adopting methods that reduce ecological footprints while satisfying growing market demands.
- Technological Innovations: Ongoing advancements in diamond synthesis techniques hint at a future where industrial diamonds are more accessible and affordable, potentially unlocking new applications we cannot fully envision today.
As noted by experts, "Understanding the multifaceted nature of industrial diamonds allows industries to innovate consistently and responsibly."
Prospects for Industrial Diamonds
The future for industrial diamonds is anything but dull. Here are several aspects that underscore their promising journey ahead:
- Emerging Markets: Countries investing heavily in mining and production are likely to bolster the sector. As these markets mature, demand for industrial diamonds will substantially rise.
- Advancements in Technology: The relationship between industrial diamonds and technology is becoming symbiotic. For instance, their applications in quantum computing and advanced optics could potentially result in breakthroughs that ripple through various sectors.
- Customization and Specialization: With ongoing research, the potential to develop specialized diamonds for niche markets is burgeoning. Tailored diamonds suited for specific tasks, like ultra-thin cutting or precision polishing, could enhance effectiveness in many fields.
- Integration with Other Materials: We might see a future where industrial diamonds are combined with other materials to create composites that have superior characteristics, enhancing performance multifold.
In sum, keeping an eye on the evolving role of industrial diamonds in both existing and emerging technologies can lead to remarkable possibilities. Their importance in industrial contexts is not merely about their physical properties but also about how they integrate with human innovation to forge new paths ahead.