Key Jewelry Bench Tools for Crafting Gemstones
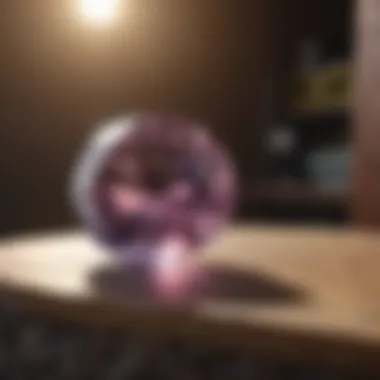
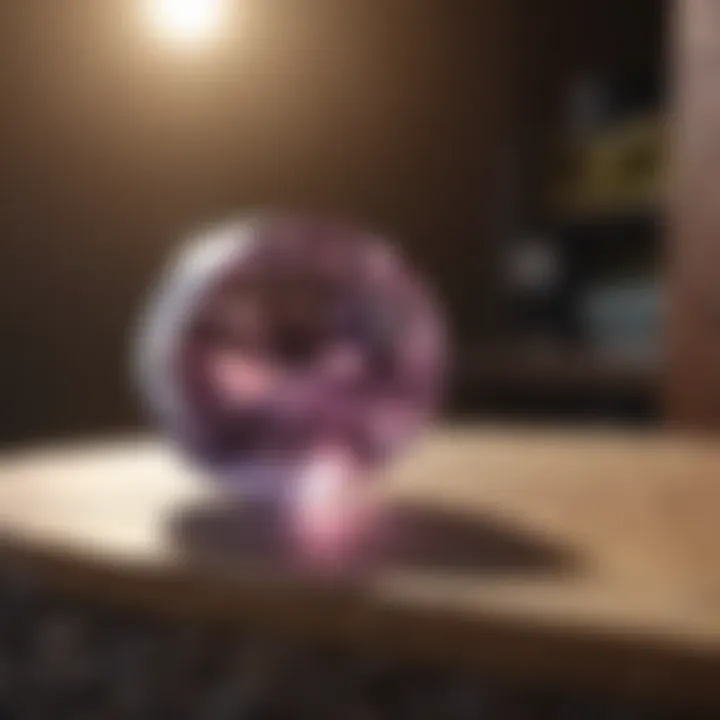
Intro
Creating stunning jewelry is not just an art; it's a marriage of skill, precision, and the right tools. For those drawn to the enchanting world of gemstones, having the appropriate bench tools is like a painter with their brush. Each instrument serves a purpose—some assist in shaping, while others ensure that gemstones are set with the utmost care. Understanding these tools is essential for enhancing craftsmanship, whether you're just starting out or are seasoned in the trade.
This article will dive into the essential jewelry bench tools specifically aimed at gemstone craftsmanship. Each section will unfold not only the tools themselves but also their applications, helping you craft with both confidence and competence.
Gemstone Overview
Definition of Gemstones
Gemstones are natural minerals or organic materials that are prized for their beauty, rarity, and durability. They can be classified based on various characteristics, including their chemical composition, crystal structure, and physical properties. A piece of jewelry with a well-set gemstone is sure to catch the eye and capture the heart, making these elements crucial in the art of jewelry making.
Classification of Gemstones
Gemstones can be generally grouped into two main categories: precious and semi-precious.
- Precious Gemstones: This category includes diamonds, rubies, sapphires, and emeralds. These stones are often more rare and sought after, often maintaining higher market value.
- Semi-Precious Gemstones: Stones such as amethyst, topaz, and garnet fall under this umbrella. While they may be more abundant, they still offer immense beauty and charm.
Clients, collectors, and craftsmen need to recognize the differences in value and utility when choosing gemstones for jewelry. Knowing what sets a piece apart enhances one's ability to communicate its worth effectively.
Historical Significance
Origins of Gemstone Use
Historically, gemstones were used not just for adornment, but also for their perceived mystical properties. Ancient civilizations valued these stones for protection against evil spirits, as symbols of power, and even for use in trade. Some cultures even believed that certain stones could foster health and prosperity. Crafting jewelry became entwined with cultural rituals and practices, thus, forming a deep-rooted connection with human civilization itself.
Cultural Insights: Gemstones in Ancient Civilizations
An examination of ancient civilizations reveals fascinating narratives centered around gemstones:
- Egyptians: Used lapis lazuli to symbolize the night sky and believed it could guide the soul.
- Greeks: Carved carnelian into seals for protection and good fortune.
- Romans: Associated emeralds with Venus and believed they could heal ailments.
These examples illustrate not just the beauty of gemstones but also the diverse meanings and values attributed to them across different cultures. This rich history serves as a foundation for modern practices.
"Gemstones are more than mere adornments; they capture human emotions, memories, and cultural heritage."
As we progress through the article, we'll detail the specific jewelry bench tools that empower artisans in their gemstone endeavors.
Prolusion to Jewelry Bench Tools
Jewelry making, especially when it comes to working with gemstones, is not merely an art; it’s a craft that demands precision and expertise. This makes the selection of tools a pivotal consideration for both novices and seasoned artisans alike. Understanding the range of jewelry bench tools available can be the difference between a dazzling piece of craftsmanship and a frustrating experience. As we delve into the essential tools, we will explore how they not only enhance the creation of beautiful jewelry but also contribute to the overall skill development of the maker.
Understanding the Importance
At the heart of jewelry making lies the intricate dance between creativity and technical expertise. Each tool on the bench has a specific purpose that facilitates the transformation of raw materials into exquisite jewelry pieces. For gemstone craftsmanship, the stakes are higher. Gems, with their unique properties and beauty, require careful handling and precise techniques.
Using the right tools can significantly reduce the margin for error. For example, using specialized pliers can help in manipulating delicate wires without marring their surface. Furthermore, an understanding of these tools helps jewelry creators make informed decisions about their workflow, ultimately leading to enhanced productivity and artistry. This comprehension navigates through the nuances of design, application, and even maintenance of the tools, enriching not just the piece being created but also the maker's confidence and capabilities.
Overview of Common Tools
The array of tools at a jeweler's disposal can be quite extensive, each serving a distinct role in the crafting process. Here are some of the most commonly used tools that one might encounter on a jewelry bench:
- Pliers: Vital for holding, bending, and cutting wires. Different types, like chain nose and round nose pliers, cater to specific tasks in jewelry making.
- Cutters: Essential for severing metal wires, ensuring clean and precise cuts.
- Files: These are crucial for smoothing out edges, shaping metals, and finishing touches that enhance the overall appearance of the piece.
- Sanding Tools: These help in polishing surfaces, often used before the final polishing process.
- Workbenches: A sturdy workbench can make all the difference in comfort and efficiency during the crafting process.
- Mandrels and Jigs: These tools assist in shaping metals and settings precisely, vital when working with gemstones.
Each of these tools, while common, plays an indispensable role in achieving the desired results in jewelry-making processes. By selecting the proper tools, craftsmen can ensure that their creations embody not just aesthetic appeal but also the intrinsic value of quality workmanship.
Essential Hand Tools
Hand tools form the backbone of any jewelry workshop, acting as the precise instruments that allow artisans to transform raw materials into finely crafted pieces. The importance of hand tools can't be overstated, especially for those delving into gemstone craftsmanship. They provide the control and finesse necessary to work with delicate stones and metals, ensuring the highest quality during the crafting process.
Each type of hand tool serves a distinct purpose, contributing to different stages of the creation process. Using the right tools not only enhances efficiency but also significantly improves the overall quality of work. Let's explore the essentials:
Pliers and Cutters
Having a set of reliable pliers and cutters can make or break a jewelry deigner's project. These tools are vital for gripping, bending, cutting, and shaping materials, often in tight spots where hands can only do so much. Here is a closer look at the specific types of pliers and cutters that are indispensable in any jewelry-making toolkit:
Chain Nose Pliers
Chain nose pliers are a staple for many jewelers due to their versatility. The narrow, flat tips allow for reaching into small spaces and making delicate bends. This makes them particularly useful when working with fine chains or small components, providing precision without the risk of damage.
One significant aspect of chain nose pliers is their ability to grasp tiny beads and embellishments, ensuring every piece aligns perfectly. Their grip is strong yet gentle, ideal for when you're working with softer materials that could otherwise be marred. While these pliers are favored for their accuracy, they might not be the best choice for heavy-duty work, which can be a slight drawback if your projects lean towards sturdier designs.
Round Nose Pliers
Round nose pliers are distinguished by their tapered, rounded tips, making them indispensable for creating rounded loops and bends in wire or metal. These pliers are particularly popular among those in gemstone craftsmanship when forming jump rings or finishing pieces. They deliver a smooth curvature, which is important for aesthetic quality in jewelry pieces.
A unique feature of round nose pliers is that they can create multiple loop sizes by simply adjusting where you grip the wire. Their versatile functionality can be a huge time-saver, but they lack the gripping mechanism found in chain nose pliers, making them less suitable for gripping smaller, delicate parts.
Cutter Tools
Every jeweler needs a reliable set of cutter tools. These are crucial for trimming wires and cutting materials to the desired lengths. High-quality cutters are designed to slice cleanly through metal, allowing for precise cuts without fraying or bending the material. Their sharp edges are what set them apart, allowing for smooth edges, particularly of thicker wires.
A significant characteristic of cutter tools is that they come in various styles, from flush cutters to side cutters, catering to different cutting needs. While flush cutters provide a clean edge and are preferred for visibility in a finished project, side cutters can handle heavier work. It's worth noting that maintaining these tools is essential; dull cutters can lead to damaged materials, undermining the craftsmanship.
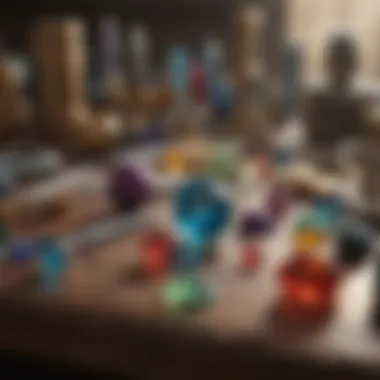

Files and Sanders
The use of files and sanders is integral for smoothing and refining after cutting, allowing artisans to prepare surfaces for polishing and setting stones. Proper tool selection and technique can greatly affect the final finish of the piece.
Types of Files
There are various types of files that serve distinct purposes in jewelry-making. Some are flat, others are round, and some are tapered. Each of these files has unique characteristics that cater to different tasks, such as shaping edges, creating grooves, or refining intricate details.
When employing files, the outcome relies heavily on using the right type for the job. For instance, a coarse file is indispensable for quickly removing excess material, while a fine file is best for the final touches, ensuring a smooth surface. In this way, files are beneficial for both rough and delicate processes of jewelry crafting, allowing for flexibility in application.
Using Sanding Tools Efficiently
Sanding tools are another essential component for achieving a high-quality finish on jewelry pieces. The goal of sanding is to smooth out rough edges and surfaces, preparing the jewelry for subsequent polishing steps. It’s essential to understand various grits of sanding paper or pads since each granularity serves different stages of the refinement process.
Particularly, medium to fine grits of sanders are highly favored for jewelry work. Employing these tools efficiently means developing a technique that balances pressure and motion—too much pressure can lead to unwanted scratch marks, while too little will not be effective in smoothing surfaces. Mastering this balance can contribute significantly to the overall effectiveness of your craftsmanship, leading to polished and professional-looking pieces.
"Investing time into understanding your hand tools can transform your work quality, taking it from good to exceptional."
In summary, essential hand tools such as pliers, cutters, files, and sanders are crucial pillars in the field of jewelry craftsmanship. They enable precise manipulation of delicate materials, ensuring that every piece tells a story with quality and craftsmanship at its heart.
Workbenches and Layouts
When it comes to gemstone craftsmanship, the layout of your workspace and the workbench you choose can shape your entire jewelry-making experience. A well-thought-out bench and organizational setup can make tasks smoother and help you focus on your artistry. The right workbench supports your tools and your processes, ensuring that each piece you create is a testament to both skill and careful planning.
Choosing the Right Workbench
Choosing the right workbench affects how comfortably and efficiently you can work. It's more than a mere platform; it's your creative command center.
Material Considerations
Selecting a workbench material is crucial in influencing its durability and performance. Hardwood benches, like maple or oak, are often regarded as the gold standard. They offer sturdiness and an inherent quality that absorbs vibrations well. This minimizes tool chatter when you're cutting or soldering, ultimately leading to cleaner finishes. Yet, hardwoods can be pricey, and maintaining them requires diligence. Alternatively, laminate surfaces offer a smooth, affordable choice but can lack the heft needed for larger operations. They’re easy to clean, though, and thus a legit option for those short on time or budget.
Design Preferences
The design of a workbench lets you tailor the space to fit your needs. Considerations like height, storage options, and whether you need a built-in vice can influence your workflow significantly. An L-shaped design, for instance, allows for multiple working angles, ideal when tackling various projects simultaneously. While a simple rectangular bench may suffice for beginner projects, as your skills elevate, you might yearn for something more sophisticated. Thus understanding which design features correspond to your crafting habits will likely pay dividends in time saved and output quality.
Organizing Your Workspace
Once you’ve settled on the right workbench, the next piece of the puzzle is organizing your tools and materials effectively. Chaos breeds frustration, and that’s the last thing you want when working with gemstones.
Tool Placement Strategies
Where you place your tools can greatly impact your efficiency. Keep frequently used items like pliers, cutters, and your magnifying lens within arm's reach. Magnetic strips can hold metal tools securely while keeping your work surface clear. Utilize drawer organizers for lesser-used items; this way, you can maintain a streamlined look and make your gear easy to find. It’s about creating a flow that minimizes unnecessary movements—an essential thought for any serious jeweler.
Maximizing Efficiency
Maximizing efficiency revolves around creating a harmonious balance between the space you have and the tasks at hand. An efficient setup saves you time. One practical approach is employing a zones system: dedicate sections of your workspace to specific activities—soldering, polishing, setting stones—so you can transition smoothly between processes. This makes it easier to allocate time effectively, allowing you to complete projects more swiftly without scrambling for misplaced tools. Ultimately, it builds habits that lead to higher productivity, giving you more time to focus on the finer details of your craft.
The right workbench and an organized workspace not only enhance efficiency but can elevate your entire jewelry-making journey, making each piece a product of careful consideration and skill.
By emphasizing the significance of choosing appropriate materials, understanding design preferences, and organizing your workspace, gemstone craftsmanship can reach previously unattainable heights.
Precision Tools for Gemstone Setting
Precision tools are often seen as the heart of gemstone artistry, playing a vital role in defining the quality and craftsmanship of intricate jewelry pieces. The importance of these tools lies in their ability to assist artisans in achieving the perfect fit and secure placement for each gemstone. When a gemstone is properly set, it not only enhances the piece’s beauty but also helps ensure durability and longevity, thus safeguarding the artisan's efforts. Mastering gemstone setting can elevate one's skills and artistry, leading to works that captivate and resonate with clients.
Mandrels and Jigs
Types and Their Uses
Mandrels and jigs represent the fundamental building blocks in the domain of precise gemstone setting. They come in various shapes and sizes, each tailored to specific jewelry applications. For instance, a ring mandrel aids in shaping rings to the desired size, while a stone setting jig holds the piece firmly in place—enabling artisans to work with precision and ease. This rigidity helps in preventing unwanted movement, which is crucial when dealing with delicate stones like opals or emeralds.
One striking aspect of mandrels and jigs is their adaptability; they can be customized to cater to unique design requirements, offering artisans the flexibility to innovate. This characteristic not only enhances procedural efficiency but also opens up new avenues for creativity, making them a favored choice among many jewelers. However, the main disadvantage may lie in the initial learning curve and the costs associated with acquiring specialized jigs.
Fabricating Custom Jigs
The craft of fabricating custom jigs is closely related to the use of standard mandrels, yet it takes precision to another level. By designing custom jigs, jewelers can simplify repetitive tasks and create tailor-made solutions to navigate unique challenges in their work. A custom jig can streamline spindle hole drilling or assist in aligning stones exactly where they need to be, ensuring each piece is fabricated consistently and accurately.
An essential aspect of custom jigs is that they allow jewelers to integrate their signature style or specific design elements directly into the setting process. This personalization can lead to a more efficient workflow, reducing the overall time spent on production while enhancing the artistry involved. However, it’s crucial to find the right balance between investement in custom fabrication and the returns, considering a jig is often only beneficial for specific tasks.
Loupes and Magnification
Choosing Optical Tools
Selecting the right optical tools is fundamental when it comes to fine craftsmanship in jewelry making. Loupes, microscopes, and magnifying glasses are among the favorites, allowing artisans to examine the minute details of gemstones and settings with clarity. A quality loupe can reveal inclusions and imperfections that are simply invisible to the naked eye, which can greatly influence the assessment and final price of the jewelry.
One of the core benefits of optical tools is their portability. Unlike bulky microscopes, a loupe can easily accompany artists to shows, allowing for accurate inspections on the go. Yet, the discerning jeweler should be aware that not all loupes are created equal; complexity in lens quality can shift a useful tool into merely a convenient piece of gear. Investing time in learning about the right brands, magnification power, and lens coatings can pay off significantly in the long run.
Importance of Proper Lighting
Amplifying the effectiveness of optical tools is proper lighting—a not-so-subtle yet crucial element in the world of gemstone craftsmanship. The right lighting can dramatically affect how stones appear under magnification, highlighting their true attributes or drawing attention to flaws that need correction.
Natural daylight is often seen as the gold standard for evaluating the quality of stones, but not every workspace is equipped for this luxury. Utilizing task lights or full-spectrum bulbs can offer illumination that allows jewels to sparkle vividly while revealing inconsistencies. Thus, a well-lit workspace can significantly elevate the precision in the setting process.
"A jeweler without proper lighting is like a painter without a canvas. Each detail counts, and so does the light they are set in."
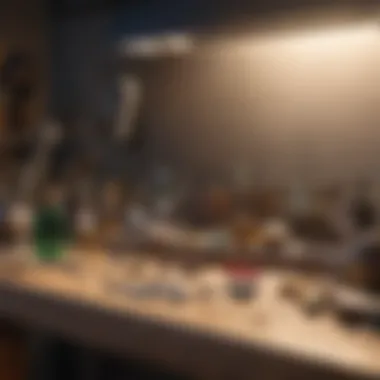
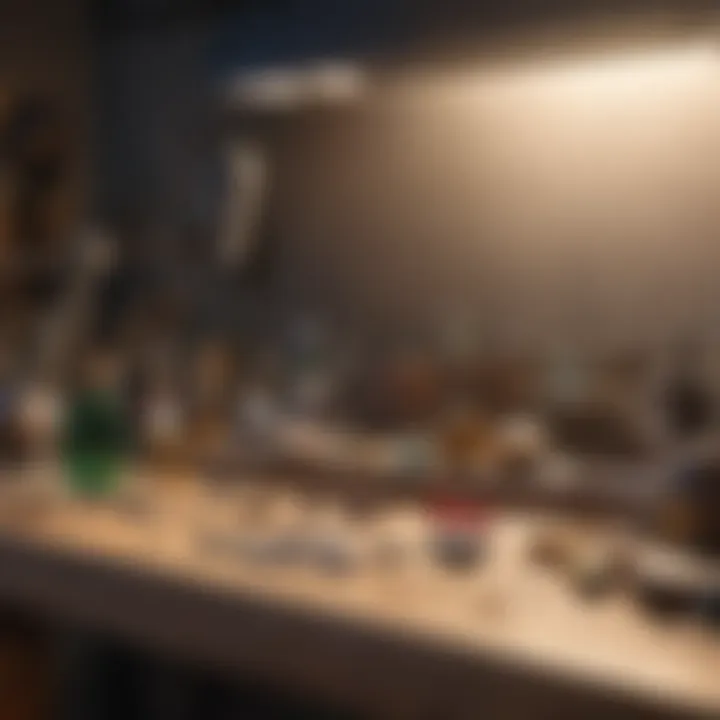
Soldering and Welding Equipment
Soldering and welding are vital components in the realm of jewelry making, especially when it comes to combining different metals and creating lasting connections. Understanding the tools and techniques specific to these processes leaves one primed for intricate designs and robust constructions.
Types of Soldering Tools
Torches and Soldering Stations
Torches serve as the lifeblood of the soldering process in jewelry making. A good torch allows for precise temperature control, which is essential for working with delicate materials, especially gemstones. The benefit of using a soldering station is the stability and security it offers, making the entire operation smoother and safer.
A popular choice among jewelers is the butane torch due to its portability and ease of use. For larger studio setups, an oxy-acetylene torch can produce a more intense flame, thus enabling the welding of thicker metals.
In the world of jewelry making, the difference between a successful project and a disaster often lies in the quality of the torch used.
Safety Precautions
With the use of high temperatures comes the inherent risk. Safety precautions should never be overlooked. Wearing safety glasses and proper clothing are basic yet critical steps. Jewelers should also be familiar with fire hazards; having a fire extinguisher nearby is a practical measure that could save both materials and lives. Furthermore, utilizing proper ventilation reduces the risk of inhaling fumes that might arise during soldering or welding processes.
The unique aspect of these precautions is not just about preventing accidents, but also about fostering a work environment that prioritizes health and safety.
Welding Techniques for Jewelry
Benefits of Welding
Welding, while often seen as a specialty technique, holds significant advantages in jewelrymaking. This method allows for seamless joins that are often stronger and more visually appealing than traditional soldering. By utilizing welding, jewelers are empowered to explore innovative designs that require the melding of various metals.
The key characteristic of welding is its ability to create a bond that maintains the integrity of both materials involved. It’s particularly beneficial for pieces that undergo stress, such as rings or bracelets, ensuring they endure the test of time.
Understanding Different Methods
Welding in jewelry can take multiple forms, including laser welding and micro-welding. Each method has its strengths and is chosen based on the project's specific needs. For instance, laser welding can be ideal for delicate work, allowing for precision without affecting surrounding areas.
On the other hand, TIG welding might be favored for work involving thicker metals due to its versatility and powerful performance.
A clear grasp of these methods broadens the jeweler’s toolkit, enabling them to select the best approach for each piece they craft. Thus, understanding different welding techniques is not just an asset, but a necessity for serious craftsmen aiming for excellence in their work.
Polishing and Finishing Tools
In the realm of jewelry making, where precision is non-negotiable, polishing and finishing tools hold sway over both the aesthetic and functional aspects of a piece. These tools do not merely aim to enhance the luster of surfaces; they transform unfinished products into radiant artifacts, sometimes seeming to breathe life into gemstones, making them shine brighter than ever. Understanding the range of polishing and finishing tools you can wield isn't just about creating visual appeal; it's integral for maintaining the integrity of the piece and assisting the artist's vision through a well-executed, professional finish.
Types of Polishers and Buffing Wheels
Choosing the Right Polisher
Choosing the right polisher is akin to finding the perfect dance partner when creating your masterpiece. You want a tool that complements your techniques while offering reliability. Electric polishers, for instance, tend to be favored due to their consistent performance and ability to handle various materials. The key characteristic here is versatility; many modern electric polishers can adjust speeds and adapt to different textures. This adaptability makes them a solid choice for most jewelers because it reduces the risk of damaging delicate components while still achieving the desired shine.
One unique feature about electric polishers is their efficiency. Hours can be saved, allowing jewelers to focus on creativity rather than getting snagged in a manual process. However, it's important to remember that with great power comes the necessity for precision—overzealous use can lead to unwanted alterations in your work.
Application Techniques
Application techniques play a critical role in how the tools are used effectively. Mastering the art of application means understanding the nuances of pressure and motion as the polisher glides across the surface. One key characteristic of effective application is consistency; maintaining even pressure leads to a uniform finish. Techniques such as circular motions or back-and-forth strokes can significantly impact the outcome, so practice here is paramount.
Different materials require different approaches; for example, a softer touch is prevalent when working on softer gemstones compared to more robust metals. The unique feature of these techniques is their capacity to make or break the final product. A well-applied polish not only elevates the beauty of the piece but also reinforces the craftsmanship involved. Neglecting these application fundamentals can lead to uneven finishes or, worse, surface damage, which can be challenging to remedy.
Finishing Products
Using Compounds Effectively
Using compounds effectively involves selecting materials that harmonize with your desired finish. Polishing compounds vary in coarseness; the choice of a fine or coarse compound can drastically alter the final appearance of your jewelry. One key characteristic here is that compounds engineered for specific materials can produce better outcomes, saving time and frustration.
Some jewelers prefer tripoli compounds for an initial polishing step, followed by a final application of rouge to achieve that mirror-like shine. The unique feature of understanding how and when to use these compounds is crucial to the process. Missteps, such as using a coarse compound on a polished surface, can result in scratches that might need additional work to remove, ultimately delaying the project.
Preserving Gemstone Integrity
Preserving gemstone integrity during the polishing process is fundamental to ensuring your creations remain true to their natural beauty. It's essential to recognize that not all gemstones can handle the same mass of pressure or heat, thus honing your technique is crucial. One key characteristic here is sensitivity; some stones, like opals or turquoise, are susceptible to damage under excessive force or inappropriate materials.
An exceptional feature of preserving integrity is the use of specialized pads designed for different types of gemstones. These pads can help mitigate risks by providing a gentler touch while achieving that necessary glow. By paying heed to gemstone properties and employing gentle techniques, you safeguard against scratches and discoloration, maintaining the stone’s original allure and value. Ultimately, understanding this element saves your work from potential ruin and enhances the overall satisfaction with your art.
"Proper polishing isn't just about making things shine. It's about showcasing the stone's story, preserving what nature created, and marrying that essence with craftsmanship."
In summary, polishing and finishing tools in jewelry making are not merely functional; they are vital in bridging the gap between raw materials and the finished artistic expression. The variations in polishers, techniques, products, and preservation methods create a complex web that jewelers must navigate meticulously. Familiarity with these elements can not only enhance one’s craftsmanship but also elevate the emotional connection between the jewelry and its eventual wearer.
Specialized Tools for Different Techniques
In the craft of jewelry making, the subtleties of various techniques can significantly affect the quality and uniqueness of the finished piece. Specialized tools come into play as vital instruments that cater to specific requirements in engraving, etching, casting, and more. Mastering these tools not only enhances a jeweler's skill set but also opens avenues for creativity and precision in their work. By understanding these specialized tools, artisans can achieve intricate designs and flawless finishes, which are essential in gemstone craftsmanship.
Engraving and Etching Tools
Manual vs. Electric Engravings
When it comes to engraving, choosing between manual and electric tools is a crucial decision that can influence the outcome of your project. Manual engraving tools such as burins offer fine control, allowing for detailed designs that might feel more personal or handcrafted. This type of engraving is favored by purists who believe that a hand-done finish holds more character. On the flip side, electric engravers can deliver consistent results more quickly, which is invaluable in a production setting. For creating delicate or intricate patterns, having the option to switch between the two techniques can be a game-changer.
Some advantages of manual engraving include:
- Greater control over the depth and pace.
- The ability to create unique textures that electric tools might struggle with.
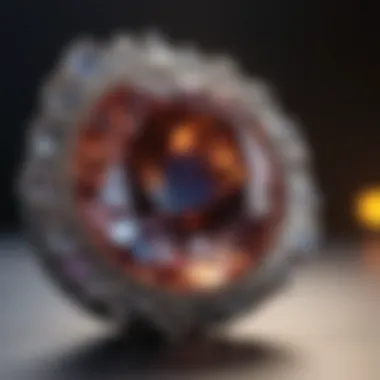
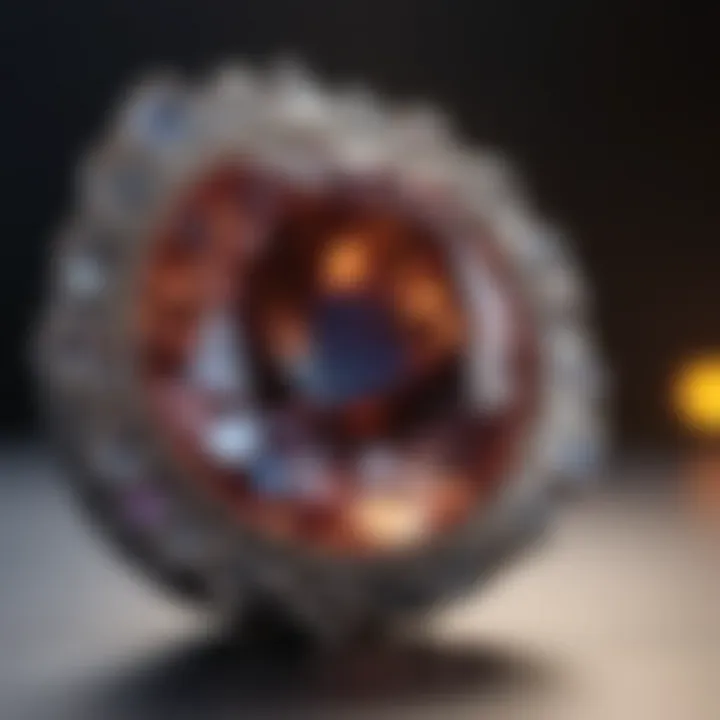
However, the disadvantage can be the time factor—manual work can be time-consuming, which might not suit every maker's pace or business model.
Choosing the Right Bits
Selecting the appropriate engraving bits is just as important as the engraving method itself. Different bits serve various purposes—from fine detail work to broader strokes. Elements like material compatibility and bit size determine the effectiveness of the engraving, making it a vital choice in the creative process. For instance, a diamond-tipped bit offers durability and precision, suitable for harder materials, while softer materials might benefit from a bur or a steel bit.
Key characteristics of choosing the right bits include:
- Compatibility with different tools to ensure efficiency.
- The ability to select sizes and shapes tailored specifically to design needs.
Using the incorrect bit can lead to issues like chipping, cracking, or an overall uneven finish, which can hinder the quality of your work. Understanding the unique features of each bit will ultimately contribute to a more polished and refined craftsmanship.
Casting Tools
Understanding Investment Casting
Investment casting stands out as a technique that allows jewelers to replicate intricate designs with a high degree of accuracy. This method involves creating a wax model, which is then encased in a ceramic shell. Once the ceramic hardens, the wax is melted away, leaving a hollow cavity. Molten metal is poured into this cavity, producing an exact replica of the original model. This process is often preferred for its ability to capture fine details, making it perfect for gemstone settings where precision is key.
The main features of investment casting are:
- Flexibility in design, allowing for both mass production and one-off pieces.
- Reduced finishing time since the cast creates a near-final piece, reducing the work needed post-casting.
However, it's vital to note that setting up an investment casting operation requires careful attention to detail and quality control, as any mistake in the shell, wax model, or pouring can affect the final product.
Required Equipment
To engage in investment casting, a jeweler must gather specific equipment. This includes a wax injector, a vacuum casting machine, and a furnace capable of reaching required temperatures for metal melting. Each piece of equipment plays a significant role in ensuring that the casting process runs smoothly and efficiently. Additionally, aspects like venting systems and safety gear cannot be overlooked.
Notable characteristics of essential casting equipment are:
- The vacuum casting machine is indispensable for preventing air bubbles, which can compromise the integrity of the casting.
- The furnace needs to match the metal you are working with to ensure uniform melting and pouring.
While acquiring this equipment represents a financial investment, the payoff is a higher quality of work, allowing artisans to push the boundaries of their creativity and craftsmanship.
Maintaining and Caring for Tools
Taking care of your tools goes beyond mere responsibility; it’s a requisite for ensuring consistency in your work. In the delicate world of jewelry making, where precision is paramount, maintaining your tools can significantly affect both the quality of your craftsmanship and the longevity of your equipment. A well-cared-for tool not only performs better but also inspires confidence in the artisan using it. The time invested in the maintenance of tools translates into lesser challenges during the creation process.
Cleaning and Storage
Proper Cleaning Techniques
Cleansing your tools after each use might seem like a chore, but it’s essential for their efficacy and your overall output. Tools that work with metals, like pliers or cutters, often gather residues—oils, dust, and tiny metal shavings—that can interfere with their function. Simple techniques, like wiping them down with a soft cloth and using appropriate cleaning fluids designed for metal, can make a world of difference. Many jewelers swear by using a gentle cleaners, as they often contain less abrasive agents that keep the tool surfaces intact.
The unique benefit of these cleaning methods is that they minimize rust and corrosion while enhancing the tool’s performance. However, it's worth noting that some solutions can be too harsh. Always make it a point to read product labels and ensure the cleaner is compatible with your specific tools to avoid damage.
Safe Storage Practices
How you store your tools can be just as critical as how you clean them. Proper storage keeps your tools organized, prevents accidents, and extends their lifespan. Using tool rolls or dedicated drawers with foam inserts are practical choices, as they can cushion your tools and keep them from rattling around. One particular feature of safe storage is magnetic strips. These can hold tools securely, while giving you quick access without digging through a cluttered drawer.
However, avoid overcrowding any storage space. Items pressed together can lead to scratches or even chipping, particularly with delicate instruments. Allocating enough space for each tool ensures easy retrieval and, ultimately, maintains their integrity.
Tool Lifespan and Replacement
Understanding the lifespan of your tools is crucial because every instrument has a breaking point. Knowing when a tool is approaching this limit allows you to make timely replacements, ensuring that your work remains top-notch and reducing the risk of mishaps during operations.
Signs of Wear
Signs of wear can present themselves in various forms, from visible nicks and dull cutting edges to more subtle clues like decreased performance. For example, if pliers start to feel less precise when gripping, it may indicate that the jaws are worn out. This could affect the quality of the finished piece, making it a critical area to monitor. Recognizing these indicators promptly can save both time and material costs, as substituting worn tools early generally prevents further complications.
Knowing When to Replace
Deciding when to replace tools doesn’t come down to a fixed timeline—that's where experience comes into play. Observing the performance and condition of your tools gives you vital cues. If a tool feels unresponsive or requires excessive physical effort to get the same results, that’s often a red flag. Furthermore, from a safety perspective, tools that show signs of extensive wear could pose risks and should be replaced immediately.
In sum, a keen eye and familiarity with your tools will aid in making these critical decisions. Investing in high-quality tools is advisable, as they generally come with longer lifespans and better performance.
"In the world of craftsmanship, the tools are an extension of the artisan’s skill. Care for them well, and they will help create wonders."
To wrap things up, maintaining and caring for your tools effectively will not only enhance your efficiency but also elevate the standard of your jewelry masterpieces. Remember, it's this seemingly mundane aspect that often makes the bigger picture shine.
Culmination
In wrapping up our in-depth exploration of jewelry bench tools, especially those necessary for harnessing the beauty of gemstones, it becomes clear that these tools are more than just metal and wood; they are an artist's paintbrush, a sculptor's chisel, and in many ways, the very heart of the jewelry-making process. Without the right instruments, even the most talented artisan would find it challenging to bring their visions to life. Each tool discussed plays a critical role in transforming raw materials into finely crafted pieces, highlighting not only precision but also creativity.
Recap of Key Points
To distill everything we've covered:
- Essential Hand Tools: Pliers, cutters, files, and sanders form the backbone of any jewelry-making toolkit. Understanding how to wield these tools effectively allows for precision in every cut and curve.
- Precision Tools: Mandrels, jigs, and loupes enhance accuracy, making sure each gemstone fits just right. Magnification aids in detecting imperfections that could hinder a masterpiece.
- Soldering Equipment: Knowing the right torches and safety measures is paramount, particularly when working with heat-sensitive materials. The difference between a sturdy joint and a messy bond often lies in the equipment used.
- Finishing Tools: Polishers and the correct compounds preserve the beauty of gemstones while also providing the professional finish that sets beautiful jewelry apart.
- Specialized Techniques: Engraving and casting require specific tools and insights that can take a craftsperson’s work from amateurish to extraordinary.
- Maintenance: Regular cleaning and understanding when tools need replacing is a sign of a true craftsman.
Practicing these key takeaways can aid jewelry makers in their journey toward skill mastery and artistry.
Future Trends in Jewelry Tools
Looking ahead, several trends are influencing the tools of the trade in jewelry making. The rise of 3D printing continues to revolutionize how complex designs can be created with minimal effort. This technology allows creators to prototype jewelry pieces quickly and with great specificity, pushing the envelope of design possibilities.
Moreover, advancements in laser engraving technology provide ultra-precise etching and detail work that was unimaginable a couple of decades ago. This not only enhances the aesthetic appeal of the jewelry but also opens doors to customization that customers increasingly seek.
Finally, the move toward sustainable practices is emerging strongly in tool manufacturing. Craftspeople are looking for tools that are not only effective but also environmentally friendly, pushing brands to innovate away from harmful materials. As these conscious consumers grow in number, demand for ethical tools will likely surge, shaping the future landscape of jewelry crafting.
In summary, understanding the essential tools, their proper care, and the trends shaping their development is crucial for anyone serious about gemstone craftsmanship. As the tools evolve, so too will the art of jewelry making, continuing to enthrall enthusiasts and collectors alike.