Understanding the Lost Wax Process: A Step-by-Step Guide
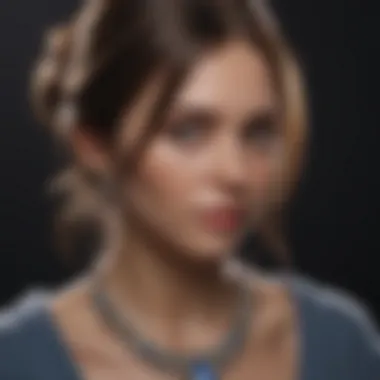
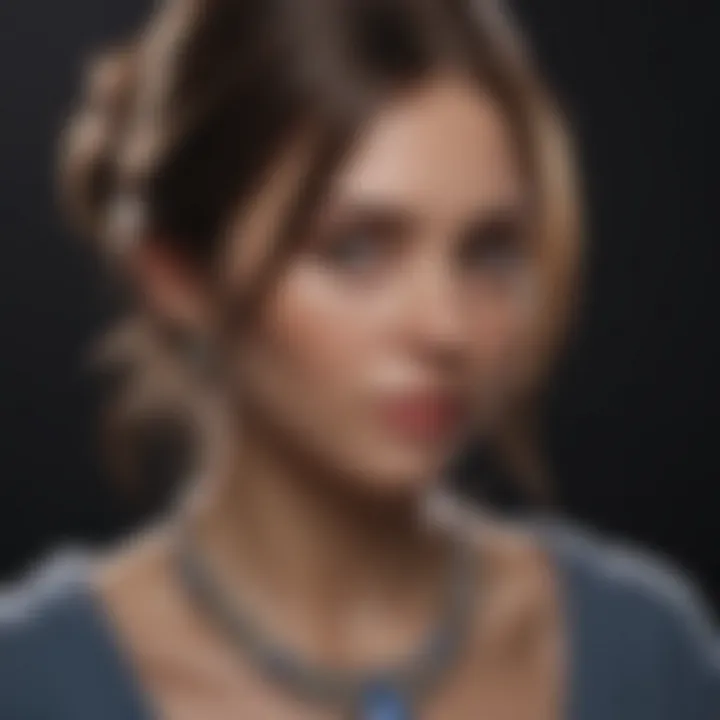
Intro
The lost wax process is a time-honored technique that has endured for centuries in the world of metal casting. From its origins in ancient cultures to its application in contemporary jewelry making and sculpture, this process remains relevant today. The subsequent sections will provide an in-depth examination of the lost wax casting, guiding readers through the various stages involved, materials used, and considerations one must keep in mind to master this technique. By understanding the intricacies of the lost wax process, artisans can enhance their craft and create pieces that resonate with both tradition and innovation.
Gemstone Overview
Understanding the context of gemstones and their role in metal casting can further enrich the knowledge of those engaged in the lost wax process. Many pieces made using this method often incorporate gemstones, providing both aesthetic value and structural integrity.
Definition of Gemstones
Gemstones refer to naturally occurring minerals or organic materials that are valued for their beauty, rarity, and durability. These materials are typically cut and polished for use in jewelry and decorative arts. Some common examples include diamonds, rubies, and sapphires. Their allure often lies in their clarity, color, and the stories they carry from the earth beneath our feet.
Classification of Gemstones
Gemstones can be categorized into two primary groups: precious gemstones and semi-precious gemstones.
- Precious Gemstones: This group typically includes diamonds, emeralds, rubies, and sapphires due to their rarity and high value.
- Semi-Precious Gemstones: Although still sought after, these stones, such as amethyst, aquamarine, and garnet, are generally more abundant and accessible.
Understanding the classification helps artisans select the appropriate stones for their creations, ensuring both aesthetic appeal and market viability.
Historical Significance
The historical background of gemstones and their use in craftsmanship is rich and intricate, often revealing much about past civilizations and their values. Exploring these aspects can further illuminate the choices of materials and techniques employed by modern artisans.
Origins of Gemstone Use
The use of gemstones can be traced back thousands of years. Early humans utilized stones for various purposes, including decoration, currency, and believed magical properties. Archaeological findings indicate that ancient Egyptians employed turquoise and lapis lazuli not only in jewelry but also in burial artifacts. The careful selection of gemstones reflects a culture's reverence for beauty and symbolism.
Cultural Insights: Gemstones in Ancient Civilizations
Ancient civilizations placed great significance on gemstones. For instance, in Mesopotamia, gemstones were often associated with deities, believed to bestow protection and favor. Similarly, in Chinese culture, jade has been considered a symbol of purity and moral integrity, traditionally used in crafts and significant life events. Such cultural insights reveal how gemstones have been interwoven with history, enhancing the narrative of the metal pieces they adorn.
Understanding the connections between gemstones and their historical significance can provide invaluable context for artisans looking to infuse meaning into their work.
The exploration of gemstones, their classifications, and historical significance underscores their importance in the realm of lost wax casting. By awakening this awareness, artisans can deepen their connection to their craft, making informed choices that align their work with historical truths and aesthetic values.
Prologue to the Lost Wax Process
The lost wax process is a pivotal technique in metal casting, essential for artists and artisans. Understanding this method is crucial because it combines artistry with precision. This process allows for intricate designs that metalworkers could not achieve through traditional casting methods. The significance of the lost wax process cannot be overstated; it not only serves historical and cultural contexts but also enables contemporary practices in jewelry making and sculpture.
Historical Context
The origins of the lost wax process date back to ancient civilizations, tracing a lineage to cultures like the Greeks, Chinese, and Egyptians. This technique evolved over centuries, from early applications in crafting ornaments to its modern use in fine jewelry. Archaeological finds show evidence of lost wax casting that spans thousands of years. Artisans created detailed and unique pieces, which also reflects their cultural narratives.
The process was often shrouded in mystery, passed down through generations. Each era refined the techniques, allowing for variations that catered to different artistic visions. Understanding this historical context enriches our appreciation for the method and highlights its enduring relevance.
Purpose and Applications
The lost wax process serves multiple purposes in the world of art and functionality. Primarily, it is used to create finely detailed metal objects. This includes items such as sculptures, jewelry, and decorative art. The ability to produce complex shapes and designs enables artists to explore their creativity without limitation.
In contemporary scenarios, the process is not limited to small-scale artisans. It is also employed in mass production contexts where precision is needed repeatedly. Different types of metals, from gold to bronze, can be cast using this method, making it versatile for various applications. Furthermore, the lost wax method remains essential for creating custom designs, which is particularly important for jewelry artists who want to express individualism in their work.
"The lost wax process bridges ancient techniques with modern innovations, making it essential for artists in various fields."
In summary, the lost wax process is important for its historical significance and practical applications in today's artistic landscape. It serves as a fundamental process for artisans aiming to create unique and intricate artwork, deserving of deeper exploration and understanding.
Materials Required
The lost wax process is a meticulous and intricate method that demands specific materials to ensure success. Each material serves a distinct purpose and contributes to the overall quality of the final product. Understanding these materials can profoundly impact the efficiency and outcomes of the casting process. Careful selection can lead to smoother procedures and superior results.
Wax Types
Wax is the foundation of the lost wax process. Different types of wax can be used, each with its own unique properties. Common options include:
- Paraffin Wax: This is a widely used wax due to its availability and ease of use. It is relatively inexpensive and easy to carve, making it a popular choice for beginners.
- Modeling Wax: This type is more flexible and durable, making it ideal for intricate designs. It holds detail well and can be reused several times.
- Carving Wax: Often used by sculptors, this wax is suitable for creating detailed models. It is tougher and can withstand more extensive manipulation.
Selecting the right type of wax can enhance the carving precision and overall durability of the model. This choice depends on the specific needs of the design and the artist’s intended outcome.
Investment Materials
Investment materials play a critical role in the lost wax process, forming the mold that captures the details of the wax model. The main options include:
- Silica Sand: Often blended with a binding agent, silica sand helps create a sturdy mold. It withstands high temperatures during metal pouring.
- Gypsum Bond: This material is beneficial for creating finer details. Gypsum molds capture intricate textures due to their fine powder composition.
- Ceramic Investment: Suitable for high-precision casting, ceramic investments are designed for metals with higher melting points.
Selecting the appropriate investment material is essential for achieving both the required detail and durability in the final casting. Each material varies in its performance and should be chosen based on the type of metal being poured and the level of detail required.
Metal Options
The choice of metal significantly affects both the physical properties and aesthetics of the final piece. Some popular materials include:
- Bronze: Known for its appealing finish and durability, bronze is often used in artistic sculptures.
- Sterling Silver: A favorite in jewelry making, this metal has a classic look and is relatively easy to work with.
- Gold Alloys: Various gold mixtures are available, allowing for a range of colors and properties depending on the alloy composition.
When selecting metals, practitioners must consider their desired aesthetic and the functional properties of the final product. Each option delivers distinct characteristics, affecting both the appearance and strength of the cast piece.
Creating the Original Model
Creating the original model is a fundamental stage in the lost wax process. It sets the foundation for the entire casting procedure. A well-crafted model can significantly impact the quality and aesthetic of the final piece. This initial step requires attention to design details, accuracy, and the material used for the model.
The importance of creating a precise original model cannot be overstated. The model essentially serves as a blueprint for the investment mold. Every detail captured in the model will translate directly into the final cast. If there are imperfections in the original, those flaws will persist in the final piece. Thus, designers must emphasize quality in both concept and execution, ensuring all features and proportions align with their artistic vision.
Design Considerations
When designing the original model, several considerations come into play. These include the intended use of the final piece, size, complexity, and the necessary detailing.
- Functionality: Is the piece primarily decorative or functional? Jewelry pieces often require a balance between form and function.
- Proportions: Keeping proportions consistent is crucial. Sketching the piece beforehand can assist in visualizing how details will scale.
- Complexity: Highly intricate designs may complicate the casting process. It's prudent to evaluate whether the details can be reproduced accurately.
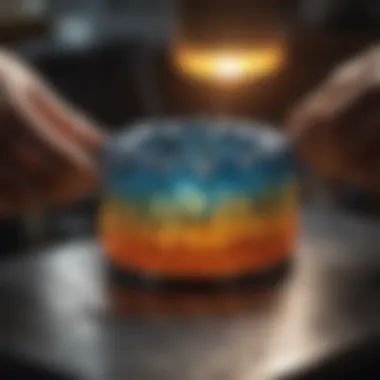
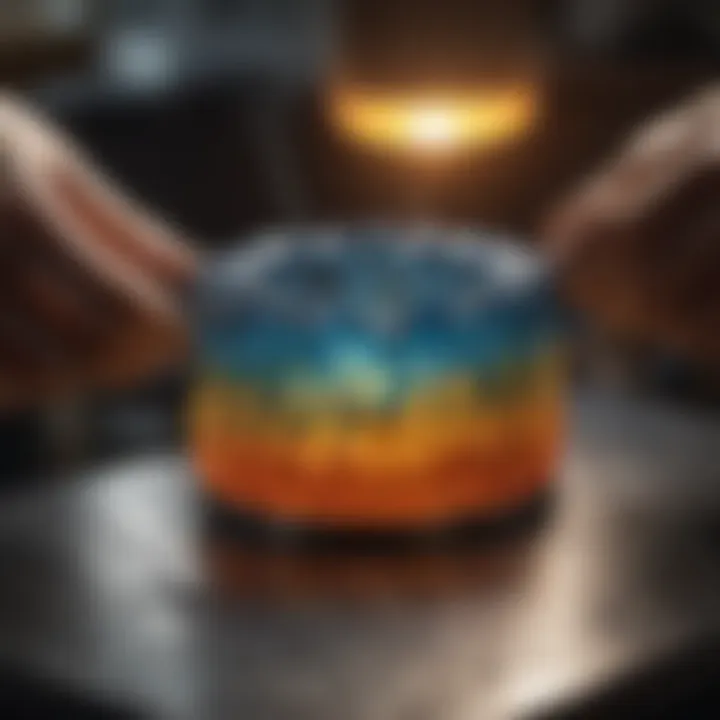
Another important consideration is the choice of material for the model. Different wax types affect how easy or difficult the model is to manipulate and refine. For instance, softer wax may allow for more precise detailing but could be prone to deformation. It is essential to select a wax that offers adequate working properties while maintaining structural integrity.
Carving Techniques
Carving techniques play a key role in transforming the design into a tangible form. Artisans have a range of tools and methods at their disposal, and the choice often depends on the complexity of the design.
- Hand Tools: Basic tools like knives and chisels can be used for finer details. These allow for intricate designs but require a steady hand and skill.
- Power Tools: For larger or complex models, power tools can expedite the process. Devices like rotary tools provide speed but must be used with caution to avoid overshooting details.
- Sculpting: For some designs, clay or other sculpting materials may also be used to create the original model before casting in wax. This can serve as a prototype.
Ultimately, the carving technique should align with both the design's complexity and the artist's skill level. Effectively executed carving leads to a more seamless transition into the investment mold, ensuring that the final cast retains the intended details and quality.
"A well-made original model is the key to a successful lost wax cast. Without it, even the best materials cannot save the final product from failure."
Artisans are encouraged to refine their techniques continually. Practicing on smaller pieces can cultivate skills before tackling significant projects. The result will be a more controllable and satisfying workflow.
As the original model is created, remember that it is not just about producing a replica. It’s a crucial stage that influences the overall success of the lost wax process.
Preparing the Wax Model
Preparing the wax model is a critical aspect of the lost wax process. This step significantly influences the final outcome of the casting. A well-prepared model guarantees that the details of the original design are transferred accurately to the final piece. The precision of this wax model can make the difference between a striking piece of jewelry and one that lacks finesse.
The preparation involves two major components: wax injection and adding details. Each of these elements contributes to the overall quality and success of the casting.
Wax Injection
Wax injection is the process of introducing molten wax into a mold, typically created using a specific wax model or pattern. This technique is paramount because it allows for the creation of highly detailed and intricate designs. The wax must be heated to a specific temperature to ensure that it flows smoothly into every part of the mold. The consistency of the wax and the temperature used can affect the precision of the final product.
One benefit of wax injection is that it reduces the chances of air bubbles forming during the process. If air bubbles get trapped in the wax, they can lead to defects in the final casting. Choosing the right wax type also plays an important role; different formulations cater to various applications and complexities in designs.
Tip: Always check the specifications of the wax you are using, as different wax types will have unique melting points and properties.
Adding Details
Adding details to the wax model is a meticulous process that requires patience and skill. This is where the artistry of the piece truly shines. Small details can enhance the overall aesthetic and value of the final casting. Techniques such as carving, engraving, and even attaching additional wax pieces can be employed to achieve the desired intricacy.
During this step, attention to proportion and symmetry is crucial. If the details are not balanced, the final piece may appear flawed. One effective strategy is to periodically step back and review the piece from different angles, ensuring that no detail goes unnoticed.
After completing the detail work, ensure that the wax model is free of imperfections. Proper sanding or polishing may be necessary to smooth out any rough areas. This will ultimately contribute to a cleaner and more professional final product.
In essence, preparing the wax model is foundational to the lost wax process. The quality and accuracy of the wax model set the stage for the subsequent steps, impacting both the technical precision and artistic beauty of the final cast piece.
Building the Mold
Creating a mold is a critical step in the lost wax process. This stage enables the transformation of the wax model into a durable metal piece. Without a proper mold, the casting will not possess the desired precision or detail. The mold supports the integrity of the final product, ensuring that every intricate element of the design is captured.
Assembly of the Wax Model
The assembly of the wax model is an essential part of mold building, as it lays the foundation for the final cast. First, ensure that all parts fit securely together. It is crucial to check for any gaps, as these can become points where molten metal leaks out or where flaws may develop. The details in the model must be carefully considered. Sometimes, adding gates or vents to facilitate the flow of metal and escape of air will improve the casting process significantly.
- Fitting together parts: Each section must align perfectly.
- Ensuring no gaps: Look for spaces that may cause leakage.
- Adding gates: These assist in the proper flow of metal.
Gates are small channels that allow the molten metal to enter the mold, while vents let air escape. Both should be planned at the beginning of the assembly process to prevent complications down the line. Additionally, regular inspection during assembly can minimize potential issues.
Investment Application
Once the wax model is assembled, the next step is applying investment material. This application surrounds the wax model completely, creating a shell that will hold the form during casting. The investment material—often a mixture of silica sand and plaster—needs to be applied evenly to ensure a consistent thickness across the model.
It’s important to follow these steps during the investment application:
- Mixing ratio: Ensure the right proportions to strengthen the mold.
- Application technique: Use a brush for hard-to-reach areas.
- Allowing for hardening: Let the investment material cure completely.
The proper investment process not only enhances the mold's strength but also facilitates a smooth finish on the final metal piece. Once set, the investment material will expand slightly during the pouring of metal, making it crucial to time everything appropriately.
"An evenly applied investment leads to a clean casting with minimal defects."
Inspect the mold after this stage to ensure integrity. Any cracks or imperfections can lead to the introduction of weaknesses in the final product. Thus, taking care during the investment application is essential for achieving a successful outcome in the lost wax process.
W Investment and Drying
In the lost wax casting process, the investment and drying stage is critical for the integrity of the final piece. This phase involves applying a material that surrounds the wax model, which will later be removed to create a mold for pouring metal. Understanding this step is vital for achieving high-quality results. Without proper investment and drying, the final piece may lack the desired detail and strength.
Allowing Proper Drying Time
The drying time plays a significant role in the quality of the cast. After the investment material is applied to the wax model, it is essential to allow sufficient time for it to dry completely. This ensures that the mold sets properly and any moisture is evaporated. If the investment does not dry sufficiently, it can lead to defects in the cast piece, such as surface imperfections or bubbles.
Several factors affect drying time, including:
- Environmental conditions: Humidity and temperature can impact how quickly the investment dries.
- Thickness of the investment: A thicker layer may require longer drying times.
- Type of material used: Different investment materials have varying drying times.
Typically, drying times can range from a few hours to several days, depending on these factors. Monitoring the drying process is essential to ensure a high-quality mold.
Importance of Layering
Layering is a technique often employed during the investment process. Proper layering contributes to the final mold's effectiveness and strength. This step involves applying multiple coats of investment material, allowing each layer to dry before applying the next one.
The advantages of layering include:
- Enhanced detail retention: Multiple layers can capture fine details from the wax model, leading to a more accurate final piece.
- Increased strength: A layered investment is generally more robust, providing better support during metal pouring.
- Reduced risk of breakage: A thick, single layer might crack under pressure, while multiple layers distribute that pressure more evenly.
Proper investment and drying are not just steps in the process; they form the foundation for successful metal casting.
Wax Removal
Wax removal is a crucial stage in the lost wax process. This phase ensures that the wax model is eliminated effectively, paving the way for the final casting of the metal piece. The removal process is not merely a technical requirement but involves careful planning to prevent damage to the final product.
Heating Techniques
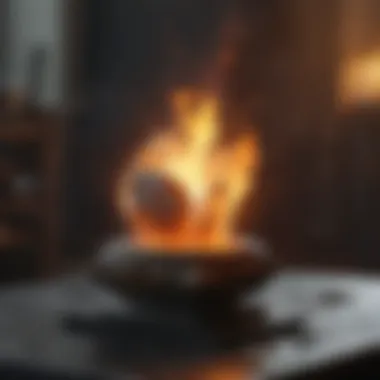
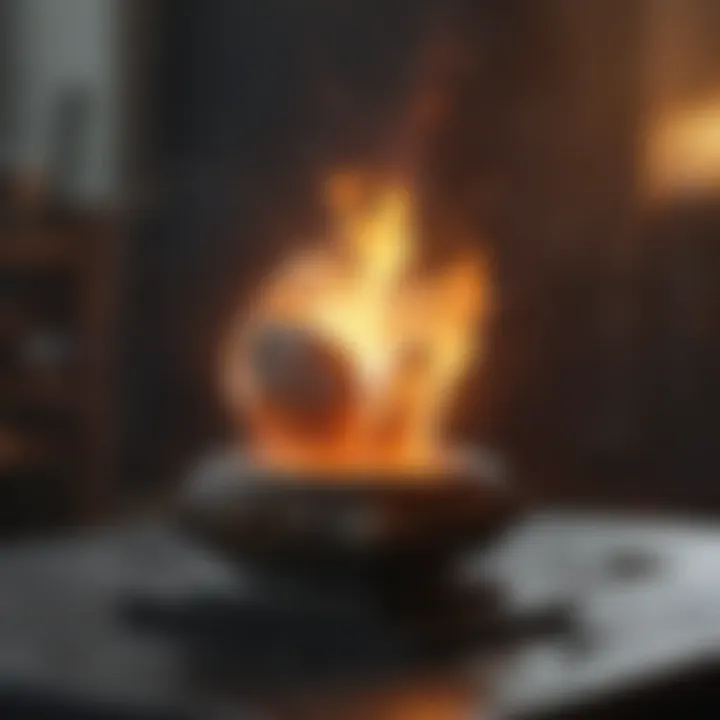
Heating techniques play a vital role in effectively removing the wax. The primary objective here is to melt the wax without causing undue stress on the mold material. A common method is to use an oven. Setting the oven to a controlled temperature ensures that the wax evaporates uniformly. Typically, the wax melts at around 140-160 degrees Fahrenheit. Therefore, it is important to monitor the temperature closely to avoid overheating the mold.
Another method involves utilizing a heat gun. A heat gun offers more precision compared to an oven, as it allows for targeted heating. This can be particularly useful when dealing with intricate designs, ensuring that the wax melts away while keeping the integrity of the mold intact.
When using these heating methods, proper ventilation is necessary. The fumes produced during the melting process can be harmful if inhaled. Working in a well-ventilated space or using a fume hood is advised.
Dealing with Loss
Dealing with loss in the context of wax removal refers to handling any wax residue that may remain in the mold. Even with careful heating, small amounts of wax can sometimes cling to the mold's internal surfaces. This residue can impact the quality of the final metal piece.
To mitigate this issue, a secondary heating may be needed. After the initial wax removal, inspecting the mold is essential to identify any remaining wax areas. If you find residue, reheating may assist in further eliminating it. However, caution is required not to damage the mold material.
Additionally, chemical solvents can be used for cleaning residual wax. Yet, they should be used with care, as they can react with investment materials. Testing solvents on a small area is recommended before full application. This will help ensure that the integrity of the mold remains intact while achieving a clean surface for metal pouring.
Metal Pouring
Metal pouring is a crucial phase in the lost wax process, where the molten metal is introduced into the mold. This stage has a significant impact on the final piece, influencing its quality and characteristics. A successful pouring process not only ensures that the mold is filled accurately but also dictates the integrity and aesthetic of the cast. Various factors need to be taken into account to optimize the pouring stage, including temperature control, the type of metal being used, and the technique employed.
Furnace Preparation
Furnace preparation is essential to guarantee that the metal reaches the right temperature for optimal pouring. Properly preparing the furnace includes a few key steps:
- Temperature Settings: Ensure that the furnace is calibrated according to the melting point of the specific metal utilized. For example, gold requires a temperature of about 1,064 °C, while silver melts at about 961 °C.
- Furnace Cleanliness: Before melting metal, it is crucial to remove any debris or leftover materials from previous casts. Residues can contaminate the new batch of molten metal.
- Crucible Selection: The choice of crucible must align with the metal type and furnace. Graphite and ceramic crucibles are common. Using the appropriate crucible material is vital to withstand high temperatures without contaminating the metal.
By addressing these dimensions, one ensures an efficient melting process that sets the stage for effective pouring.
Pouring Techniques
The technique used during metal pouring can greatly affect the outcome of the cast. The following techniques are often employed:
- Direct Pouring: This method consists of pouring the molten metal directly from the crucible into the mold. It requires steady hands and confidence to prevent spillage or uneven distributions.
- Gated Pouring: Here, a gate or channel is created in the mold, allowing the metal to flow through controlled paths. This is beneficial to reduce turbulence and avoid air pockets.
- Tilt Pouring: In this approach, the crucible is tilted to pour the metal. This technique gives better control over the flow and can minimize oxidation when using certain metals.
Ultimately, the pouring method selected should correspond with the desired properties of the final piece. Adapting the technique to the specific requirements of the project ensures a successful pour, leading to a high-quality cast that meets the creator’s vision.
"Pouring is not merely a step; it is a critical art that shapes the very essence of each unique piece."
The completion of the metal pouring stage lays the foundation for cooling and subsequent finishing steps. The outcomes of this process resonate through the entire work, underscoring its importance in the broader lost wax casting framework.
Cooling Process
The cooling process is a critical stage in the lost wax casting procedure, determining the quality and integrity of the final metal piece. It comes after the metal pouring and must be approached with both precision and caution. An appropriate cooling regimen ensures that the poured metal solidifies uniformly, maintaining the desired properties and structural integrity of the casted piece. This section elaborates on the essential aspects of cooling, focusing on timing and techniques to minimize defects during this pivotal phase.
Time Considerations
Time is of the essence during the cooling process. Each metal type has its unique cooling rate, which affects the final outcome. Factors such as the thickness of the piece, environment temperature, and the metal used all influence how long the cooling will take.
The thicker the item being cast, the more time it requires to cool adequately. If left to cool too quickly, it can result in stresses within the metal. Ideally, artisans should allow the piece to cool slowly, promoting uniform temperature distribution and reducing the risk of warping.
It is also advisable to monitor the cooling process closely. Some metals may benefit from being placed in a controlled environment, avoiding extreme temperature fluctuations. A good practice is to wait for the metal to reach ambient temperature naturally before any handling occurs. This helps prevent sudden thermal shocks.
Avoiding Cracking
Cracking is one of the most significant concerns during the cooling process. Uneven cooling can lead to internal stresses that manifest as cracks, which compromise the piece's aesthetic and structural integrity. Several measures can be employed to mitigate this risk.
First, preheating the mold can help minimize thermal shock. This technique ensures that the metal does not encounter an abrupt temperature change. Additionally, continuous cooling methods can be implemented, allowing the piece to cool more predictably.
The use of metal alloys with greater ductility can also be beneficial. Ductile metals can absorb more stress, thereby reducing the likelihood of cracking. Furthermore, the cooling speed should be consistent. Abrupt cooling, such as dunking the piece in water, should be avoided until the metal has cooled adequately.
"Understanding and managing the cooling process is essential for successful casting. Proper time management and techniques can prevent significant defects, ensuring a high-quality piece."
Finishing the Casted Piece
The finishing process of the casted piece is crucial for achieving the desired aesthetic and functional qualities in metalwork. This stage not only impacts the overall appearance but also influences the piece's marketability, especially within the jewelry sector. A well-finished piece reflects the skill of the artisan and enhances the piece's value. Understanding how to effectively finish your casting is essential for anyone looking to elevate their craftsmanship.
Removing Investment Material
Removing the investment material is the first step in finishing your casted piece. The investment serves as a mold and must be carefully chipped away or dissolved, depending on the materials used. This removal can be done manually with tools like brushes and hammers or through chemical processes if a soluble investment was employed. Here are important points to remember:
- Assess the type of investment material used. This determines the removal method.
- Use protective gear like gloves and goggles, as pieces can break off unexpectedly.
- Work in a clean area to avoid unnecessary contamination.
Pay attention to details such as corners and fine areas that might hold residual investment material. Leaving any remnants can detract from the final appearance and quality of your piece.
Polishing Techniques
Polishing is vital for achieving a smooth and shiny finish that can dramatically enhance the casted piece's appeal. Various techniques can be employed, including:
- Mechanical Polishing: Utilizes specialized tools such as rotary polishers, which can provide a high-gloss finish. This method is suited for larger pieces or where speed is necessary.
- Hand Polishing: Best for intricate details, hand polishing allows for precision in hard-to-reach areas. Common materials include cloth and fine polishing compounds.
- Electrolytic Polishing: This method involves an electrochemical process that can yield exceptionally smooth surfaces. It is ideal for pieces where high detail and finish quality are paramount.
In addition to polishing, consider:
- Using a buffer with increasingly finer grits to avoid scratches.
- Testing on a similar but less valuable piece first, if you are unsure of the technique's effectiveness.
"Finishing techniques not only improve the appearance but also prepare the piece for final applications, increasing its durability and desirability."
The finished product should exhibit a gleam that reflects the skill of the artisan while being durable for wear or display. A thorough understanding of both removing investment material and polishing is essential for those looking to create exceptional products in the world of metal casting.
Quality Control
Quality control in the lost wax process is crucial for ensuring that the final casted pieces meet the standards expected by artisans and clients. This section delves into the specific elements of quality control, outlining its benefits and considerations.
Maintaining high quality in casting involves rigorous inspection at multiple stages of the process. Early detection of mistakes can save time and resources. Consistent quality ensures that the end product is not only aesthetically pleasing but also structurally sound. A commitment to quality can enhance a brand's reputation, fostering trust among customers.
Inspection Criteria
Inspection criteria serve as guidelines that help identify acceptable and unacceptable outcomes. During each phase of production, certain aspects are scrutinized:
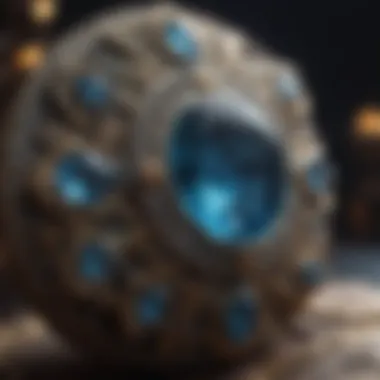
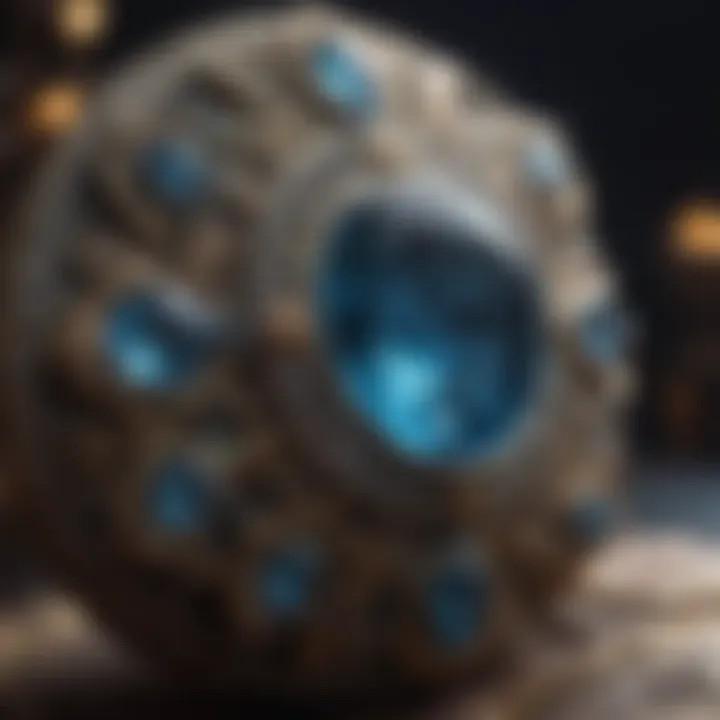
- Surface Texture: The finish should be smooth and free of blemishes. Any imperfections can detract from the beauty of the piece.
- Dimensions: Accuracy in sizes and proportions is vital. This is where measurements during the model stage must be checked against the final output.
- Weight: The mass of the finished product should align with expected outcomes based on the investment material and metal used.
- Structural Integrity: Cues such as cracks or voids within the piece can indicate weak spots, which might jeopardize durability.
Implementing a clear checklist for these criteria helps artisans maintain consistency.
Common Defects
Identifying and addressing common defects is another essential aspect of quality control:
- Air Bubbles: These can form in the investment material, causing weak points.
- Unwanted Surface Marks: Scratches or other marks from handling can compromise the product's overall look.
- Inaccurate Details: Missing features can occur if the wax model was not properly created or finished.
- Porosity: Excessive porosity can lead to undesirable surface quality and structural weakness, which should be addressed early.
To mitigate these defects, techniques such as improving wax model preparation and perfecting investment application are necessary.
In summary, rigorous quality control practices are vital in ensuring the integrity and beauty of casted pieces. Paying careful attention to inspection criteria and being aware of common defects leads to a more refined final product.
Applications in Jewelry Making
The lost wax process plays a pivotal role in the realm of jewelry making, seamlessly combining artistry with precision. This ancient technique is not merely a method of metal casting; it embodies a journey from concept to finished piece. Understanding its applications offers insights into how artisans can create unique, high-quality jewelry while preserving a level of detail and craftsmanship that is often unattainable through other methods.
Custom Designs
One of the most compelling aspects of the lost wax process is its capacity for custom designs. Artisans can craft intricate and personalized pieces that reflect individual creativity. The wax model allows for a great degree of detail, making it possible to incorporate unique textures, patterns, and shapes that resonate with personal or client specifications. This adaptability is particularly valued in bespoke jewelry. Each piece emerges from a tailored approach, meaning that customers receive jewelry that feels singular and special. This customization engenders a closer connection between the jeweler and the client, fostering relationships based on trust and satisfaction.
Furthermore, the ability to modify designs in the wax stage means that any adjustments can be made before the metal is poured. Artisans can thus refine and iterate on their designs, ensuring that the final product aligns with their vision. Such flexibility contributes significantly to the artistic freedom found in modern jewelry making.
Mass Production Considerations
While the lost wax process is often associated with custom and one-of-a-kind pieces, it also accommodates mass production under the right circumstances. Many jewelry makers have devised strategies to utilize this technique for larger runs. To achieve efficiency in mass production, studios often invest in wax replication technologies, allowing for the creation of multiple wax models from a single original.
This method can drastically reduce the time needed per piece while maintaining high standards of quality. However, it is critical to ensure that each replicated model preserves the fine details that are characteristic of the lost wax method. This introduces challenges in quality control, as maintaining consistency across numerous pieces becomes paramount.
In the context of mass production, considerations such as material choice, investment material layering, and casting temperature become important. Each step must be optimized to ensure both speed and quality are balanced effectively. Adopting a mass production focus can ultimately broaden the market appeal for artisans and enable them to reach wider audiences without sacrificing their unique style.
The lost wax process in jewelry making bridges the gap between craftsmanship and innovative mass production, offering versatility that satisfies varied market demands.
Challenges and Solutions
The lost wax process is a complex procedure that, while time-honored, many artists encounter several obstacles. These challenges are vital to understand for anyone looking to achieve finesse in their work. The solutions often revolve around optimizing the techniques and materials used. Knowing the common hurdles can help practitioners make informed choices and adjustments that enhance their results.
Technical Difficulties
Technical difficulties arise from various aspects of the process. One prevalent issue is maintaining the correct temperature during wax removal. If the temperature is too high, it can lead to damaging the mold, while too low can result in incomplete wax evacuation. Both scenarios are detrimental to the integrity of the final cast.
Management of heat sources during metal pouring is equally crucial. Inconsistent heating can result in improper metal flow, affecting the detail and strength of the cast. Rotating furnace positions may be necessary for better results; however, this requires careful planning and setup.
Another hurdle is the precision required in creating the mold. Errors in the mold can lead to deformities in the final product. Manufacturers should focus on ensuring that their mold-making techniques, such as using consistent investment materials and investing sufficient time to set the mold properly, are up to standard.
Material Limitations
When it comes to materials, several limitations can affect the outcome of the lost wax process. The selection of wax is crucial; various types have different melting points and behaviors. For instance, softer waxes might be easier to carve but have lower resistance to deformation under heat. Therefore, the selection should match the needs of the intended design.
Investment materials also have their limitations. The ability of the investment to withstand the heat during metal pouring is essential. If it cannot withstand the temperature required for certain metals, it may crack or fail, leading to loss of the cast.
Additionally, the qualities of the metal being used must be considered. Certain alloys may introduce issues like brittleness or unexpected expansion during cooling. Understanding these characteristics can save time and resources. Adjustments in the mix or alternate metals may be required based on the specific project demands.
Ultimately, addressing these challenges and understanding the solutions is crucial for anyone pursuing excellence in the lost wax process.
By acknowledging these technical difficulties and material limitations, artisans can refine their approach and improve their craft. Practitioners should be willing to experiment and adapt their methods depending on the challenges encountered.
Future of the Lost Wax Process
The future of the lost wax process is a topic of great significance. As this method has been used for centuries, it stands at an intersection of tradition and modern innovation. This blend can lead to enhanced techniques and wider applications in various fields such as jewelry making, art casting, and industrial applications. Understanding these changes helps artisans and enthusiasts appreciate the ongoing evolution of this age-old practice.
Technological Innovations
In recent years, technological advancements have revolutionized the way the lost wax process is utilized. Innovations in casting equipment and materials have made the process more efficient and accessible.
- 3D Printing: One notable advancement is the integration of 3D printing technologies. This allows artisans to create highly detailed models that were previously difficult or impossible to achieve. Printing the pattern in a wax-like filament provides a new dimension to design possibilities.
- Digital Tools: The use of CAD (Computer-Aided Design) software has also streamlined the design process. Artisans can now visualize and modify their creations with precision before physical casting begins. This minimizes material waste and reduces the number of prototypes needed.
- Advanced Investment Materials: There are now investment materials designed specifically to withstand higher temperatures. These advanced materials reduce casting imperfections and enhance the surface finish of the final product.
These technological innovations support the continued relevance of the lost wax process. They offer artists and designers an opportunity to push the boundaries of their creativity while retaining the core techniques of traditional methods.
Sustainability in Practices
Sustainability has become a crucial consideration in all forms of craftsmanship, including metal casting. The lost wax process is no exception, and efforts are underway to implement more sustainable practices without sacrificing quality.
- Recyclable Materials: New investment materials are being developed to be more environmentally friendly. Some companies are focusing on recyclable or biodegradable investment solutions, minimizing the environmental footprint of the process.
- Energy Efficiency: Technological improvements also contribute to energy efficiency. Modern furnaces are designed to require less fuel and produce less waste heat, leading to a greener casting process.
- Source of Metals: The sourcing of metals used in casting is another critical area. There is a growing trend to use recycled metals, which reduces the need for mining and contributes to conservation efforts.
Implementing these sustainable practices not only addresses current environmental concerns but also appeals to a more conscious consumer. Artisans who prioritize eco-friendly methods can enhance their brand reputation and attract a dedicated customer base.
Culmination
The conclusion serves as a vital component of this guide, encapsulating the essence of the lost wax process while highlighting its significance in both artistic creation and skilled craftsmanship. Understanding this process is essential not just for those involved in jewelry making and sculpture but also for enthusiasts wanting to grasp the full scope of metal casting techniques. The emphasis here is on how the lost wax process combines artistry with precision, resulting in pieces that are not only visually stunning but also structurally sound.
A thorough grasp of this methodology allows practitioners to replicate their finest work reliably, ensuring consistency in quality and design. Additionally, by mastering the standards and techniques discussed, artisans can push the boundaries of their creativity. The benefits of adopting the lost wax method are manifold, ranging from improved aesthetics to durable and unique designs.
"The lost wax process stands as a testament to the harmony between artistry and technology, transcending time to retain its relevance today."
Summary of Key Points
In this article, various facets of the lost wax process have been explored:
- Historical Context: Insight into the origins of the process provides a deeper appreciation of its evolution.
- Materials and Techniques: An examination of essential materials like wax, investment compounds, and metals enhances understanding of their importance.
- Steps to Success: Each step, from model creation to the final casting, emphasizes careful execution, ensuring quality output.
- Challenges and Innovations: Addressing common difficulties and discussing advancements highlights the ongoing relevance of this age-old craft.
With the knowledge gained from this guide, practitioners can confidently approach the lost wax process, utilizing both traditional and modern techniques with enhanced proficiency.
Encouragement for Practitioners
To all artisans, whether newcomers or seasoned professionals, the journey through the lost wax process offers continuous opportunities for learning and improvement. Embrace the challenges that come with mastering this intricate method. While some aspects may seem daunting, each struggle leads to growth and skill enhancement.
Build upon the techniques presented in this guide, while also adding your personal creativity. Experimenting and refining your approach can often yield unexpected delights in your finished pieces. Collaboration with other craftsmen and engaging in community discussions can also provide valuable insights.
Finally, remember that innovation is often born from tradition. Use this ancient technique as a foundation for your modern artistry, blending the past with the present to create works of art that resonate on multiple levels. In pursuing mastery of the lost wax process, you not only uphold a rich history but also push the boundaries of your craft into the future.